Изготовление воздухоподогревателей
Применение воздухоподогревателя приводит не только к увеличению КПД котла, но и при заданной производительности котла размеры топочной камеры заметно уменьшаются в случае применения подогрева воздуха.
Воздухоподогреватели по конструкции разделяются на:
• рекуперативные (трубчатые);
• регенеративные (вращающиеся).
Трубчатые воздухоподогреватели
Трубчатый воздухоподогреватель состоит из сварных секций (трубчатых кубов), представляющих собой конструкцию из труб, соединенных между собой трубными досками, и элементов перепускной системы с входящими в нее перепускными коробами, щитами обшивки, компенсаторами, опорными рамами и т.д.
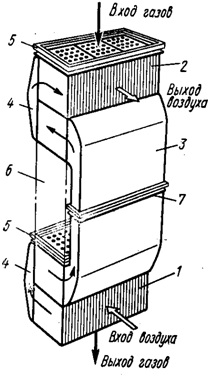
На схеме рекуперативного воздухоподогревателя: 1-нижние кубы воздухо-подогревателя; 2-верхние кубы воздухо-подоревателя; 3,4-перепускные короба; 5,7-компенсаторы; 6-место установки водяного экономайзера.
Подогрев воздуха в трубчатых воздухоподогревателях достигает 450 С. Воздухоподогреватель располагается в конвективной шахте котла за водяным экономайзером или в рассечку с ним. Горячие дымовые газы, проходя внутри труб, отдают свое тепло через стенки труб воздуху, который омывает трубы снаружи.
Основными деталями трубчатого воздухоподогревателя являются трубные доски и трубы. Материал для изготовления узлов и деталей воздухоподогревателя выбирается в зависимости от параметров газовой и воздушной среды.
Для изготовления трубных досок, работающих при температуре газов до 500 С, применяется толстолистовая углеродистая горячекатаная спокойная и полуспокойная сталь обыкновенного качества.
Если трубные доски воздухоподогревателя работают при температурах 500-550 С, то для из изготовления применяются малоуглеродистые стали марок 16ГС, 09Г2С,10Г2С1.
Воздухоподогреватели изготавливаются из стальных труб с наружным диаметром 40 и 51 мм при толщине стенки 1,5 мм. Трубы изготовляются электросварными со сварным швом вдоль всей трубы. Эти трубы могут поставляться длиной до 9 метров. Все трубы должны выдержать гидравлическое испытание при давлении 60 атм.
Внутренний грат на сварном шве должен быть удален на заводе-изготовителе.
Трубные доски
Заготовки трубных досок могут вырезаться как механическим способом, так и газопламенной резкой при условии обеспечения необходимой формы и размеров.
Резка механическим способом производится на гильотинных ножницах. газопламенная резка может выполняться вручную или газорезательным полуавтоматами и автоматами. Наиболее распространенным способом вырезки заготовки трубной доски является резка на газорезательном автомате или полуавтомате, так как в этом случае обеспечивается хорошее качество реза в сочетании с достаточно высокой производительностью резки.
Резка на гильотинных ножницах позволяет получить хорошее качества реза, но она затруднительна при больших габаритах трубных досок.
Торцы и наружная поверхность трубных досок должны быть чистыми, без трещин, закатов, раковин, окалины и расслоений. Если подобные дефекты имеют место, то они удаляются пологой вырубкой или зачисткой. Ширина такой выборки не менее пятикратной глубины. Глубина выборки дефектного места не должна выводить толщину листа на пределы минусового допуска на толщину листа.
Кромки деталей после резки должны быть ровными. Наплывы и неровности после газовой резки, заусенцы после резки на гильотинных ножницах зачищаются шлифовальной машинкой или зубилом. Большие выхваты на кромках после газовой резки могут быть исправлены подваркой этого места ручной электродуговой сваркой и последующей зачисткой шлифмашинкой.
Если трубная доска имеет большие габариты или для удобства раскроя листа возможно изготовление трубной доски из нескольких частей, но не более трех. В этом случае отдельные части доски свариваются встык двусторонним швом. Усиление сварного шва удаляется заподлицо с основным металлом. Сварка производится под слоем флюса без разделки кромок на флюсовой подушке. В случае необходимости снятия фаски на кромке трубной доски эта операция выполняется на кромкострогальном станке.
В процессе выполнения операций резки, сварки и снятия фасок трубная доска и ее кромки коробятся, поэтому перед сверлением обязательно делают правку трубных досок на многовалковых правильных вальцах. Волнистость трубных досок не должна превышать 2 мм.
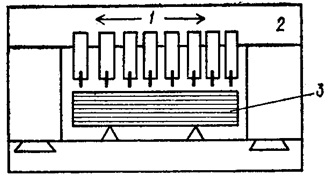
Трубная доска по своим габаритам изготавливается с допуском 3-4 мм, при этом разность диагоналей не должна быть более 5 мм.
Технология изготовления трубных досок должна обеспечить совпадение всех трубных отверстий в комплекте трубных досок каждого куба воздухоподогревателя. Поэтому перед сверлением отверстий трубные доски подбирают в пакеты, причем в каждом пакете количество трубных досок и их расположение в пакете (верхняя, промежуточная, нижняя) соответствует чертежу этого куба (секции). Скомплектованный пакет трубных досок крепится посредством струбцин, или трубные доски прихватываются между собой электросваркой через сборочные планки. Толщина пакета, подаваемого на сверление обычно не более 100 мм. Сверление отверстий в трубных досках производится по разметке верхней трубной доски пакета или по кондуктору. Для сверления последующих пакетов вместо кондуктора может быть использована трубная доска просверленного пакета. После сверления обязательно удаляют заусенцы у кромок отверстий.
Сверление трубных досок производят на радиально-сверлильных или многошпиндельных станках.
Трубы
На поверхности труб не допускаются трещины, закаты и глубокие риски. Величина грата, остающегося после сварки труб на заводе-поставщике, не должна быть более 0.5 мм. Концы труб обрезаются под прямым углом, заусенцы и рванины не допускаются. Вмятины на трубах величиной не более 50 мм по длине и 1.5 мм по глубине могут быть оставлены без изменения.
Трубы, перед тем как попасть на сборочный стенд, проходят операцию обрезки. Как правило, трубы обрезаются в необходимый размер и подаются на сборку, где больше их не подрезают. Но в некоторых случаях, при недостаточно отлаженной технологии резки, трубы обрезаются с припуском, который подрезается после сборки секции воздухоподогревателя. Подрезка концов труб производится при помощи специальной резцовой головки, установленной на пневмомашине.
Существует много технологических приемов резки труб. Технология резки труб во многом зависит от технологии присоединения труб к трубным доскам. Требования к соединению: это соединение должно быть прочным и плотным, чтобы исключить перетечки воздуха в дымовые газы. Обычно трубы соединяются с трубными досками при помощи сварки. Торец трубы должен быть чистым от заусенцев, рез перпендикулярен оси трубы, труба не должна выступать за трубную доску и утопать в ее отверстии более чем на 1мм. Уменьшение внутреннего диаметра трубы после обрезки не должно превышать допуск на овальность трубы.
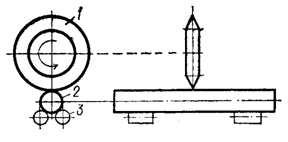
Наиболее прогрессивным и распространенным способом резки труб воздухоподогревателя является резка давящим роликом, позволяющая автоматизировать этот процесс. В качестве инструмента здесь используется ролик 1 диаметром 200 мм, толщиной 10 мм из сталей 40Х, 5ХВС, Х12ФГ. Ролик затачивается так, чтобы угол при его вершине составлял 15-25. Машинное время резки трубы 2 диаметром 40 мм с толщиной стенки 1.5 мм составляет 2 с при частоте вращения 170-200 об/мин. При резке концы трубы несколько обжимаются за счет усилия давящего ролика 1 и опорных роликов 3, но это не оказывает вредного влияния на качество соединения труб с трубными досками, если ужим трубы не превышает 1 мм. Существенным недостатком этого способа резки труб являлось значительное вспомогательное время на подачу трубы и удаление трубы после резки. Эти операции не были механизированы, что снижало производительность станка. Поэтому были разработаны различные конструкции автоматов, имеющих несколько обрезных головок.
Созданию автоматов способствовало то обстоятельство, что способ резки труб методом пластической деформации, кроме высокой производительности имеет ряд других преимуществ:
1. Конструкция отрезных головок с роликом значительно проще отрезных головок с резцами.
2. Отрезные головки с роликом не требуют сложной наладки при эксплуатации.
3. Транспортирование заготовок осуществляется в направлении, перпендикулярном оси заготовки, чем обеспечивается короткий путь перемещения и, следовательно, значительно уменьшаются габариты установки.
4. Легко осуществляется одновременная резка несколькими отрезными головками.
5. Инструмент для резки отличается исключительной простотой, дешевизной и высокой стойкостью.
Сборка и сварка кубов (секций)
Сборка секций воздухоподогревателя производится на сборочных стеллажах. В первую очередь устанавливаются на стенде трубные доски (верхняя, промежуточная, нижняя) на расстояниях, указанных в чертеже. Доски устанавливаются вертикально на ребро, и закрепляются временными технологическими раскосами из уголков и обрезков труб. Такая технология установки трубных досок непроизводительна и не всегда обеспечивает должное качество сборки. Электроприхватки, с помощью которых крепятся временные раскосы к трубной доске и стеллажу, портят трубную доску и стеллаж. В дальнейшем приходится срубать и зачищать эти прихваты с трубной доски и стеллажа. Участок в этом случае захламлен обрезками уголков и труб, используемых как подпорки и выбрасываемых потом в металлолом; нарушаются проходы между стеллажами, так как везде громоздятся раскосы.
Для обеспечения качественного выполнения работ и увеличения производительности труда следует оснащать сборочные стеллажи передвижными винтовыми или пневматическими зажимами, в которых закрепляются трубные доски. После установки доски проверяются отвесом на вертикальность и рулеткой проверяется расстояние и диагонали между досками. После выверки установки трубных досок устанавливается между досками несколько «труб жесткости» диаметром 133 мм с толщиной стенки 4 мм. Количество их зависит от размеров секции. Эти трубы придают секции первоначальную жесткость. После приварки этих труб каркас секции еще раз тщательно проверяется по всем важнейшим размерам, при этом допускается непараллельность трубных досок 4 мм, допуск на высоту секции и расстояние между трубными досками также лежит в этих пределах. Разность диагоналей не должна быть более 6 мм. Отклонение вертикальной оси секции, замеряемое по отвесу, не может быть более 6 мм.
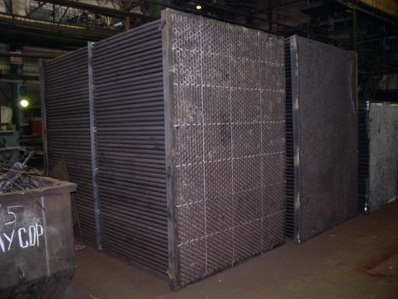
Если конструкция секции не предусматривает установку «труб жесткости», то между трубными досками сначала устанавливают несколько труб, называемых «маяковыми». Это те же нагревательные трубы воздухоподогревателя, установленные по периметру трубной доски и несколько штук в середине для придания секции добавочной жесткости.
Набор труб секции производится только после установки «труб жесткости» или «маяковых» труб и проверки каркаса секции по геометрии.
Набор труб производится вручную бригадой, состоящей обычно из двух человек. Один их них проталкивает трубу через отверстие верхней трубной доски, другой встречает трубу в отверстии нижней трубной доски. Трубы на сборку поступают не идеально прямые, они могут иметь прогиб, и поэтому труба, прошедшая через отверстие верхней трубной доски, не всегда точно попадает в отверстие нижней трубной доски. В этом случае второй рабочий направляет ее в нужное отверстие с помощью металлического прутка диаметром 10 мм. Трубы устанавливаются заподлицо с трубной доской. Выступ или заглубление конца трубы допускается в пределах 1 мм. Собранная таким образом секция подлежит обварке концов труб к трубной доске.
Операция приварки труб может быть проведена в разных положениях:
— при горизонтальном расположении трубной доски;
— при вертикальном расположении трубной доски.
Оба метода имеют свои положительные и отрицательные стороны. При горизонтальном расположении трубной доски улучшаются условия для сварки, имеется возможность более качественно выполнить эту ответственную операцию. Но в этом случае появляется необходимость кантовки секции, причем не один раз.
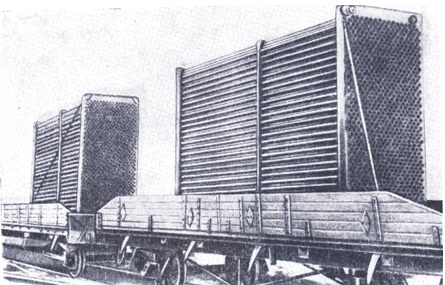
При выполнении сварных швов в горизонтальном положении каждая труба должна быть прихвачена к трубной доске до установки секции в вертикальное положение для того, чтобы трубы не выпали при кантовке. Помимо того, что кантовка громоздкой и тяжелой секции (размеры 2,5х2,5х7 м, вес до 17 т) является нежелательной операцией, следует учитывать, что при кантовке, как бы аккуратно она не проводилась, нарушаются геометрические размеры секции и, что особенно важно плотность сварных соединений приварки труб к трубным доскам. При производстве сварки с горизонтальным расположением трубных досок необходимы по крайней мере три кантовки секции, так как надо выполнить сварку на двух трубных досках, и третью кантовку вынуждены делать потому, что отправить секцию в вертикальном положении не позволяют железнодорожные габариты.
Принимая во внимание все вышеизложенное, следует считать более приемлемым способ приварки труб к трубной доске при вертикальном ее положении. В этом случае кантовки секции полностью отпадают. При этом несколько усложняется процесс сварки, однако при достаточной квалификации и навыке сварщиков качество работ не вызывает сомнений. В этом варианте полностью отпадает операция прихватки труб к трубной доске. Приварка труб при вертикальном положении трубной доски является, безусловно, более производительным и прогрессивным способом.
Обварка труб ведется сверху вниз в два приема с перекрытием начала и конца шва на постоянном токе обратной полярности. Для уменьшения деформации трубных досок от сварочных напряжений обварку труб производят в определенной последовательности отдельными участками.
После сварки поверхность трубных досок и сварных швов зачищается от брызг, шлака и наплывов от сварки.
Качество сварки труб с трубными досками должно обеспечивать герметичность их соединения. Контроль плотности приварки труб к трубным доскам каждой секции, кроме внешнего осмотра, осуществляют одним из трех способов:
1. Гидравлическим давлением 5 кПа в нижнем положении швов.
2. Опрессовкой воздухом давлением 5 кПа.
3. Испытанием керосином.
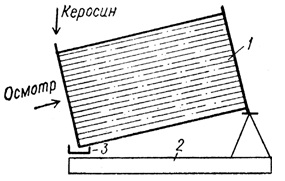
Наиболее универсальным и производительным из них является третий способ. Опыты показали, что если установить секцию под углом 15-20 к горизонтали (угол между осью труб и горизонталью) и обильно поливать керосином поверхность нагрева, то результаты испытания будут такими же, как и при нижнем расположении сварных швов приварки труб к трубным доскам, но кантовать секцию при этом не требуется, а условия для внешнего осмотра будут лучшими.
По этой причине проверку плотности сварных швов секции воздухоподогревателя керосином ведут на заводах при наклонном положении секции 1, для чего ее устанавливают одной трубной доской на подставку стенда 2 с углом наклона осей труб к горизонтали 20, а другой (проверяемой) опирают на противень 3, в который стекает керосин с внутренней поверхности трубной доски. Наружную поверхность проверяемой трубной доски покрывают меловым раствором, чтобы о местах дефектов сварных швов можно было судить по появлению жирных темных пятен керосина. Существенным недостатком этого способа является его пожароопасность.
Проверка герметичности сварных швов гидравлическим давлением столба воды 2 высотой около 500 мм (первый способ) сложна тем, что для испытания каждого типоразмера секции 1 воздухоподогревателя необходимо отдельное приспособление, при контроле требуется кантовать секции и, кроме того, неудобен осмотр сварных швов.
Контроль давлением воздуха (второй способ) применяют только при проверке специальных конструкций секций воздухоподогревателя, которые имеют плотную металлическую обшивку.
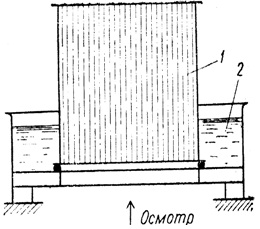
При проверке поверхность трубной доски покрывают мыльным раствором и по мыльным пузырям обнаруживают дефекты в сварных швах.
Изготовленная секция подлежит окраске и маркировке.
Отделка и транспортировка секций
После проведения испытания на плотность секция поступает на окончательную отделку. Секции воздухоподогревателя в целях предотвращения коррозии окрашиваются. Окраске подлежит доступная часть труб с наружной стороны по периметру секции.
Трубные доски и внутренняя часть труб на доступную глубину покрываются консервирующей смазкой. При температуре продуктов сгорания более 5000С верхние трубные доски покрывают теплоизоляционной мастикой. Секции воздухоподогревателя на время транспортировки и хранения со стороны трубных досок закрываются толем или деревянными щитами.
Окончательно изготовленная и принятая ОТК секция не должна отличаться от чертежа по высоте более чем на 4-6 мм. Допускается непараллельность трубных досок в этих же пределах. Допуск на расстояние между трубными досками составляет ±5 мм. Разность диагоналей секции не должна превышать 6-8 мм. На трубной доске каждой секции выбивается клеймо сварщика и ОТК. На секции прикрепляется маркировочная бирка с указанием:
• наименования заказчика;
• наименования завода-изготовителя;
• номера заказа;
• номера чертежа;
• номера места;
• веса;
• станция отправления и назначения.
Отправка секций воздухоподогревателя производится без дополнительной упаковки.
Изготовление насадок
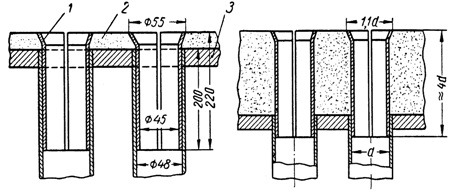
Для защиты сварных швов приварки труб к трубной доске от агрессивного воздействия золы дымовых газов в отверстия верхней трубной доски устанавливают насадки. Насадка представляет собой отрезок той же трубы воздухоподогревателя длиной примерно 150-200 мм с выбранным по всей длине цилиндра пазом шириной 14 мм. Один конец отрезка трубы развальцован на «колокольчик». Насадки изготавливаются из отходов труб воздухоподогревателя.
Изготовление насадок полуавтоматизировано. Полуавтомат выполняет следующие операции:
1. прорезку продольного паза шириной 14 мм в заготовке длиной 155 мм;
2. развальцовку одного конца насадки на конус.
Отрезка прямой заготовки производится вне этого полуавтомата. Производительность станка для изготовления насадок около 500 штук в час. Работа полуавтомата непрерывная, не требующая дополнительных переключений механизмов в процессе работы.
Насадки, изготовленные на полуавтомате, не нуждаются в каких-либо доводочных операциях и сразу поступают на комплектовку для отправки заказчику. Насадки отправляются отдельно от секции воздухоподогревателя в ящике.
Технологический маршрут изготовления секции воздухоподогревателя:
1. Разметка и резка заготовок трубных досок.
2. Обработка кромок трубных досок.
3. Сверление отверстий в трубных досках.
4. Резка труб.
5. Сборка секции.
6. Сварка секции.
7. Окраска (консервация), маркировка и упаковка секции.
Трубчатые воздухоподогреватели достаточно просты и дешевы в изготовлении, но с увеличением единичной мощности котлоагрегатов они становятся громоздкими и металлоемкими. Кроме того, трубчатые воздухоподогреватели очень чувствительны к сернистой коррозии. Поэтому все чаще находят свое применение (особенно на газомазутных котлах) воздухоподогреватели регенеративного типа. При тех же тепловых показателях РВП занимают меньший объем, имеют меньший вес и менее страдают от сернистой коррозии, чем ТВП.
Однако стоимость вращающегося регенеративного воздухоподогревателя выше равноценного по теплосъему трубчатого воздухоподогревателя.
Вращающиеся регенеративные воздухоподогреватели (РВП)
Конструкция регенеративных воздухоподогревателей позволяет легко компоновать их со всевозможными формами и размерами газового и воздушного трактов. Обычно котлоагрегат имеет два воздухоподогревателя, включенных параллельно в газовый тракт, при этом расположенные рядом друг с другом позади котла, они занимают место, равное ширине котла. Например, для котлоагрегата производительностью 320 т/ч каждый из воздухоподогревателей имеет диаметр около 5 м, высоту примерно 3 м и вес более 100 т.
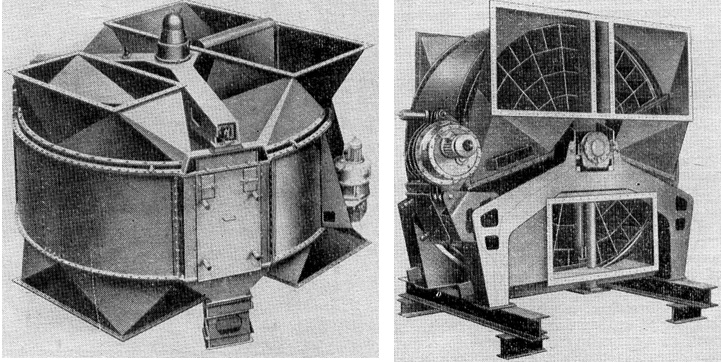
Регенеративный воздухоподогреватель может быть с вертикальным и горизонтальным расположением ротора.
При горизонтальном расположении ротора он лежит на двух радиальных подшипниках, при вертикальном вес ротора передается на балку специальной конструкции. Регенеративные вращающиеся воздухоподогреватели с вертикальной осью получили широкое применение в современных газомазутных котлах.
Принцип работы регенеративного воздухоподогревателя
Дымовые газы, уходящие из котла, проходя через пластины (набивку) вращающегося ротора, нагревают их и уходят в дымовую трубу. В результате вращения ротора нагретые пластины перемещаются на диаметрально противоположную сторону воздухоподогревателя и попадают в зону воздухопроводов.
Проходя через нагретые пластины, воздух, нагнетаемый дутьевыми вентиляторами, нагревается, а пластины охлаждаются.
Одновременно с этим происходит нагрев дымовыми газами пластин, находящихся в потоке газов.
Регенеративные воздухоподогреватели изготовляются в различных модификациях, отличающихся конструкцией привода:
• шестеренчатый – центральный привод;
• цевочный – периферийный привод;
типами уплотнений и некоторыми другими конструктивными особенностями.
Количество оборотов различных типов РВП колеблется от 3 до 4 об/мин.
Воздухоподогреватель с центральным приводом состоит из вращающегося ротора 1, закрепленного на вертикальном валу 2, который поддерживается верхней подшипниковой опорой 3. средняя 4 и нижняя 5 подшипниковые опоры вертикального вала служат для восприятия радиальных (горизонтальных) нагрузок на вал, которые возникают при работе воздухоподогревателя, а также для соединения вертикального вала с редуктором привода.
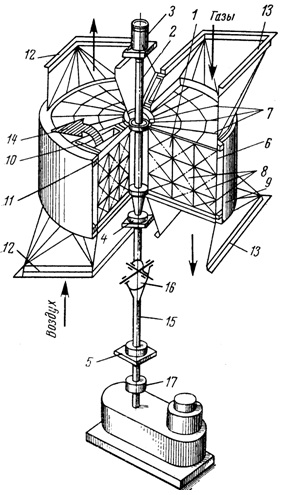
Вращающийся ротор заключен в неподвижную обечайку 6, которая опирается на каркас воздухоподогревателя. Внутренняя часть ротора делится радиальными ребрами 7 на 24 сектора 8, в которых установлены пакеты листовой набивки. Боковая поверхность 9 регенеративного воздухоподогревателя после окончания монтажа покрывается слоем изоляции. Боковая поверхность, верхняя и нижняя крышки образуют неподвижный корпус воздухоподогревателя. Для отделения воздушной стороны ротора от газовой внутри корпуса на крышках устанавливаются радиальные 10 и периферийные 11 уплотнения. К верхней крышке корпуса приварены воздушный 12 и газовый 13 короба, которые присоединяются соответственно к воздухопроводу и газоходу.
Отсос горячего воздуха, отсекаемого в промежутках между воздушным и газовым трактом, производится через окно 14, соединяемым с трактом горячего воздуха.
Главный вал ротора соединяется с редукторным приводом при помощи промежуточного вала 15 через шарнирное соединение 16 и муфту 17.
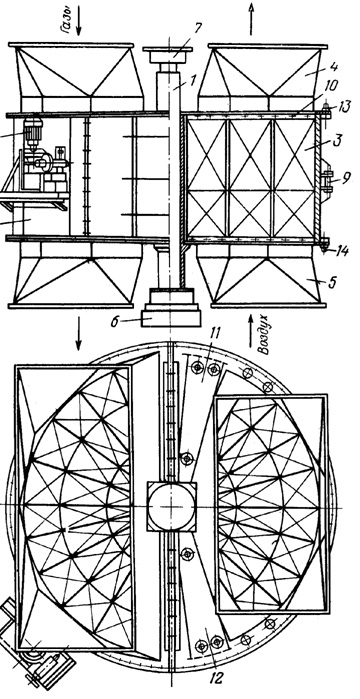
1-вал ротора; 2-корпус; 3–секция набивки; 4-короб отвода горячего воздуха; 5-короб подвода горячего воздуха; 6-нижняя опора; 7-верхняя опора; 8-привод; 9-цевочный обод; 10-полоса верхнего радиального уплотнения; 11,12-разделительные плиты; 13,14-верхнее и нижнее наружные периферийные уплотнения.
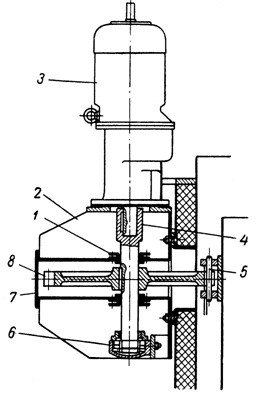
1-корпус сальника; 2-опора; 3-электродвигатель с редуктором; 4-вал; 5-цевочное колесо; 6-радиальный подшипник; 7-смотровое отверстие; 8-ведущая шестерня.
Периферийный привод воздухоподогревателя состоит из электродвигателя с редуктором 3, на валу которого установлена ведущая шестерня 8, входящая в зацепление с цевочным колесом 5, укрепленным на вращающемся роторе.
В зависимости от конструкции воздухоподогревателя и вида сжигаемого топлива температура газов перед воздухоподогревателем составляет 300-400 С, а за воздухоподогревателем 120-140 С. Регенеративный воздухоподогреватель рассчитан на подогрев воздуха до 250-350 С.
По сравнению с трубчатыми регенеративные воздухоподогреватели имеют существенно меньшие габариты и массу.
Для сравнения: расход металла для изготовления трубчатого воздухоподогревателя составляет 1,2 т на 1 т пара, вырабатываемого котлом, а при использовании регенеративного воздухоподогревателя на 1т пара расходуется 0,7 т металла.
К недостаткам регенеративных воздухоподогревателей следует отнести:
• усложнение условий эксплуатации и обслуживания (недостаток присущий любому вращающемуся механизму);
• регенеративные имеют большие присосы воздуха через уплотнения, величина присосов зависит от качества уплотнений и достигает 10-30%;
• плохо работают на сильно запыленных дымовых газах (ротор быстро забивается золой), для нормальной эксплуатации РВП снабжаются устройствами для обдувки и промывки ротора.
Материалы
Детали и узлы воздухоподогревателя изготавливаются из обычных конструкционных углеродистых сталей, кроме деталей уплотнения, которые изготавливаются из вязкой легированной стали марки Х18Н10Т. Листы набивки изготавливаются из углеродистых сталей с повышенными требованиями к качеству поверхности листов.
По конструкции регенеративные воздухоподогреватели можно разбить на:
• разъемные;
• неразъемные.
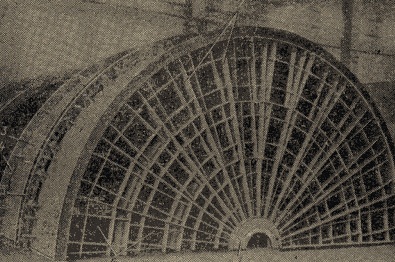
Регенеративные воздухоподогреватели для котлов производительностью более 200 т/ч имеют диаметр ротора более 4 метров и не могут быть доставлены на монтаж в целом виде так как не проходят в железнодорожный габарит. Поэтому ротор и корпус такого воздухоподогревателя делают разъемными из нескольких частей, габариты которых определяются условиями железнодорожных перевозок.
Диаметр ротора воздухоподогревателя для котла паропроизводительностью 160 т/ч равен 3600 мм, его высота 2000 мм, и он может транспортироваться в целом виде.
Технология изготовления основных узлов. Основными частями регенеративного воздухоподогревателя являются: корпус с установленными на нем опорами; ротор, разделенный перегородками на ячейки, заполненные пакетами с листами набивки; верхняя и нижняя плиты с газовыми и воздушными коробами; привод; уплотнения; верхняя специальная балка с верхним подшипником; несущая весь вес РВП; обдувочные и промывочные устройства.
Корпус неразъемного РВП представляет собой цилиндрическую обечайку с верхним и нижним фланцами. Обечайка изготавливается из листа толщиной 10-12 мм путем вальцовки с последующей сваркой и калибровкой.
Фланцы могут изготавливаться или вырезкой из листа отдельных секторов с последующей сваркой, или гибкой из полосы на вертикальных вальцах. Сборка и сварка обечайки с фланцами не представляет сложностей и выполняется обычными приемами.
Особое внимание нужно обращать на плоскостность фланцев.
Корпус разъемного РВП также является обечайкой с фланцами, но состоит из нескольких соединяемых между собой на болтах частей. На корпусе установлены опоры, с помощью которых РВП монтируется к металлоконструкциям котлоагрегата, и подставки, на которые опирается верхняя несущая балка с подшипником.
Корпус РВП должен быть плотным, поэтому сварные швы тщательно проверяются внешним осмотром. Верхняя и нижняя соединительные плиты состоят из листа толщиной 30 мм с установленными на ней коробами, к которым присоединяются газовоздухопроводы. Сварные швы коробов также должны быть плотными и проверяются на плотность с помощью керосина. Основное требование, предъявляемое к плитам – плоскостность. Прогиб плиты и другие отклонения от плоскости должны быть в пределах 2 мм. При наличии оборудования необходимо проводить механическую обработку плоскости плит, так как без обработки с помощью правки очень тяжело добиться требуемой плоскостности. В противном случае зазор между плитами и ротором будет выше допустимого, не будет обеспечена нормальная работа уплотнений и перетечки воздуха резко возрастут. Верхняя и нижняя плиты крепятся к соответствующим фланцам корпуса на болтах.
В неразъемном РВП ротор состоит из наружной обечайки и ступицы, соединенных между собой рядом ребер, установленных радиально. Кроме того, радиальные ячейки делятся на более мелкие установкой поперечных ребер. В целях обеспечения точной конфигурации ротора сборку обечайки и ступицы с ребрами производят в кондукторе. Установленные таким образом детали прихватывают электросваркой и после этого ротор поступает на сварку.
Приварку ребер к обечайке и ступице ведут на кантователе с осью вращения, расположенной горизонтально. Ввиду большого количества сварочных работ возможна подводка ротора от сварочных напряжений. В этом случае ротор принимает вид многогранника, что недопустимо на верхней и нижней кромках ротора, так как в этих местах устанавливают периферийные уплотнения. Чтобы избежать этого, концы ребер у верхней и нижней кромок обечайки не проваривают, и обечайка по кромкам сохраняет цилиндрическую форму.
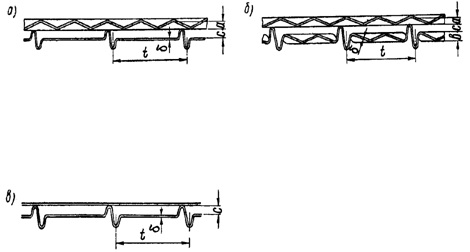
Профили набивок:
а) набивка горячей части с плоским дистанционирующим листом; б) набивка горячей части с волнистым дистанционирующим листом; в) набивка холодной части.
В ячейки ротора устанавливают пакеты с листами набивки? состоящими из нескольких гофрированных тонкостенных листов толщиной около 1 мм, соединенных между собой скобами и планками. Гофры имеют сложную конфигурацию и изготавливаются прокаткой на специальных двухвалковых профилировочных вальцах.
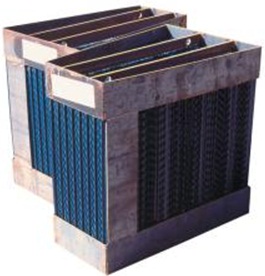
Сборку листов в пакеты производят в кондукторе, позволяющем обеспечить их поджатие в нужный размер. Необходимо обеспечить изготовление пакетов строго определенного размера с тем, чтобы при набивке ротора не возникало затруднений в установке пакетов по ячейкам.
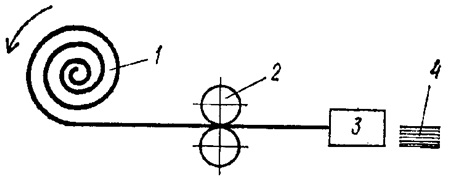
Листы набивки являются массовыми деталями. Лист сматываясь с рулона 1, поступает в профилировочные валки 2, обрезается на станке 3 в необходимый размер и сбрасывается в контейнер 4.
При цевочном приводе ротор имеет снаружи два фланца, между которыми устанавливают с определенным шагом цевки. Шаг установки цевок должен быть выдержан с точностью 0.3 мм, поэтому сверление отверстий во фланцах под цевки производят после приварки фланцев к ротору одновременно в обоих фланцах по кондуктору.
Контрольная сборка и обкатка РВП
На заводе-изготовителе обязательно проводится контрольная сборка и обкатка изготовленного РВП. С целью выявления и устранения всех недостатков изготовления. Для этого имеются специальные стенды, оснащенные необходимой оснасткой.
Контрольная сборка неразъемного РВП начинается с установки корпуса и нижней соединительной плиты. Корпус устанавливается на опоры стенда, которые заранее выверены по горизонтали. Нижний подшипник как правило не устанавливается на его место ставят подпятник, который является частью сборочного стенда. После установки корпуса в него вводят ротор без набивки. Вал может быть собран с ротором предварительно вне стенда. Ротор удерживается в корпусе на приспособлениях для подъема ротора. Выставив ротор по вертикали и отцентровав, начинают укладывать пакеты набивки. Пакеты перед установкой взвешивают и маркируют. Взвешивание пакетов производится для обеспечения равномерной их укладки по диаметру ротора и устранения перекоса ротора по весу. При необходимости зазоры между пакетами и ребрами ротора закладываются гофрированными листами набивки. Оканчивается сборка установкой верхней соединительной плиты и балки с приводом.
Для отделения воздушной стороны ротора от газовой и уменьшения присосов внутри корпуса и на плитах РВП устанавливаются уплотнения. Они являются одними из самых ответственных узлов РВП. Уплотнения могут быть различных модификаций и разделяются на:
• периферийные (окружные), которые служат для снижения присосов холодного воздуха в РВП извне;
• радиальные (торцевые), предназначенные для предотвращения перетоков воздуха с воздушной стороны в газовую.
Окружные уплотнения устанавливаются или по кромкам обечайки ротора, или на корпусе РВП. Уплотнения представляют собой набор пластин из стали марки Х18Н10Т толщиной 1-2 мм, которые крепятся с помощью болтов через овальные пазы.
Торцевые (радиальные) уплотнения устанавливаются на верхних и нижних кромках радиальных ребер ротора.
Перед установкой уплотнений необходимо проверить зазор между торцевыми кромками ротора и плитами. Зазор должен быть равномерным, в противном случае работа уплотнений будет неудовлетворительной. Проверка зазора и установка уплотнений производится через газовоздушные короба. Если конструкция ротора имеет верхний и нижний фланцы, окружные уплотнения устанавливаются на обечайку, высотой 50 мм, приваренную внутри корпуса. Уплотнения, установленные на болтах к этой обечайке, скользят по фланцу ротора.
Торцевые уплотнения часто устанавливаются на верхней и нижней соединительных плитах и регулируются с помощью рычагов с грузами. Для нормальной работы торцевых уплотнений необходимо, чтобы торцевой бой ротора был в пределах 3 мм.
В корпусе РВП имеются большие окна для возможности выема пакетов набивки при их замене. В этих окнах устанавливаются так называемые боковые уплотнения, которые часто изготавливаются регулируемыми.
Регулировку зазоров, подгонку уплотнений, центровку ротора лучше проводить до загрузки ячеек ротора пакетами набивки. После всех регулировочных операций начинают набивку ротора пакетами набивки, которые предварительно взвешены и промаркированы. Схему набивки ротора пакетами передают на монтаж вместе с паспортом РВП.
При демонтаже РВП обязательно маркируются все узлы и детали с тем, чтобы на электростанции сборка производилась в том же порядке.