Изготовление поверхностей нагрева — часть 1
Поверхности нагрева являются основной частью любого котла как по своему весу, так и по доле трудоемкости при изготовлении его на заводе.
Под поверхностями нагрева здесь понимаются трубные элементы, работающие под давлением и образующие поверхности нагрева пароперегревателя, водяного экономайзера, топочных экранов, а также водо- и пароперепускные трубы.
Применяемые материалы
Змеевики пароперегревателя и водяного экономайзера, как правило, изготавливаются из труб диаметром 25-38 мм, трубы экранов обычно имеют диаметр 60 мм, а водо- и пароперепускные трубы – диаметр 108-133 мм.
Марка применяемой стали и толщина стенки трубы зависят от тех параметров, при которых работает данная труба. Для труб экрана и змеевиков водяного экономайзера, а также водоопускных труб в подавляющем большинстве случаев применяют сталь 20, для изготовления змеевиков пароперегревателя и пароперепускных труб служат стали марок: 20, 12ХМФ, 12Х1МФ, 15ХМ, 12Х2МФСР, Х18Н9Т, Х18Н12Т и им подобные.
Трубы диаметром от 57 до 133 мм изготовляются горячекатаными. Трубы диаметром от 10 до 108 мм холоднотянутыми, холоднокатаными и теплокатаными. Горячекатаные трубы поставляются длиной не более 12 м, холоднокатаные и теплокатаные трубы могут быть длиной до 18 м.
Трубы внутри и снаружи защищается от коррозии на время транспортировки и хранения в течение 6 месяцев. Защитное покрытие не должно содержать масел.
Если контроль труб физическими методами выполнен в достаточном объеме, то гидравлическое испытание на заводе-изготовителе можно не производить, но и в этом случае завод гарантирует, что трубы выдержат необходимое давление.
Трубы поставляются партиями. Под партией труб понимаются трубы одной марки стали, одной плавки, одного размера, прошедшие термическую обработку в одинаковых условиях. Количество труб в одной партии – не более 200 штук. На каждом конце трубы диаметром 25 мм и более, толщиной стенки не менее 3 мм на расстоянии 200-300 мм от конца клеймом наносится маркировка: марка стали и номер партии. Концы труб диаметром до 133 мм плотно закрываются пластмассовыми колпачками.
Трубы поступают на котлостроительный завод в железнодорожных вагонах без специальной упаковки, кроме труб аустенитного класса, которые упаковываются в деревянные ящики.
Подготовка труб к производству
К надежности работы поверхностей нагрева предъявляются очень жесткие требования, так как любой случай нарушения их нормальной работы ведет к останову котла, что связано с большими материальными потерями, особенно на котлах большой мощности. Поэтому к качеству металла труб следует относиться очень требовательно. К сожалению, нередки случаи, когда на котлостроительных заводах или, что еще хуже в процессе эксплуатации выявляются дефекты труб металлургического характера. В связи с этим на всех крупных котельных заводах имеются цехи входного контроля труб перед запуском их в производство.
Входной контроль начинается с внешнего осмотра труб снаружи и изнутри. Трубы визуально контролируются по наружной поверхности с целью обнаружения глубоких рисок, вмятин, трещин, закатов, расслоения и тому подобного. Осмотру подвергается каждая труба по всей поверхности, изнутри трубы диаметром более 70мм осматриваются перископом.
Затем применяются неразрушающие методы контроля, такие как УЗД и магнитная дефектоскопия. Эти методы позволяют обнаружить как внутренние, так и поверхностные дефекты металла труб. Обязательной операцией входного контроля труб является — проверка марки стали труб. Для этого проводят стилоскопирование.
К операциям подготовки труб следует также отнести такие операции, как очистка труб от ржавчины и сортировка.
Достаточно часто на котельные заводы поступают трубы, имеющие значительную коррозию снаружи и изнутри. Для нормального хода дальнейшего производства трубы необходимо очистить от ржавчины. Коррозия снаружи и изнутри может быть удалена химическим путем (промывка кислотой). Однако такой способ удаления ржавчины требует организации сложного травильного хозяйства с кислотными и щелочными ваннами, промывкой труб и т.д., поэтому на котельных заводах этот метод не нашел своего применения.
Наружная ржавчина удаляется с труб на специальных станках, представляющих собой пару круглых вращающихся металлических щеток и рольганг для подачи труб. Снятая ржавчина отсасывается в приемник пыли. Иногда такой станок дополнительно оборудуется газопламенной горелкой, которая устанавливается до щеток. При нагреве трубы часть ржавчины отлетает, т.к. чистый металл и ржавчина имеют разные коэффициенты линейного расширения. Окончательная очистка трубы осуществляется металлическими щетками.
Наружная окалина хорошо может быть удалена пескоструйной обработкой труб, поэтому этот метод очистки труб от ржавчины находит все большее применение в различных установках.
Имеются установки, производящие очистку наружной поверхности труб с помощью иглофрез. Впервые такая установка появилась на ЗИО, далее на БиКЗ, БКЗ и других.
Труднее удалить внутреннюю ржавчину из труб. Для этой цели на некоторых заводах применяют ворошители. При ворошении часть ржавчины внутри трубы опадает, и она удаляется путем продувки труб сжатым воздухом. Пыль улавливается в приемник пыли. Конечно, этот метод далеко не совершенен, но он без помех позволяет вести изготовление трубных элементов. Следует иметь ввиду, что перед эксплуатацией трубные поверхности проходят на электростанции кислотную промывку для очистки внутренних полостей поверхностей нагрева котла.
Если трубы после очистки от ржавчины по каким-либо причинам не могут быть запущены в производство, то необходимо произвести пассивацию очищенных поверхностей для предотвращения коррозии.
В последнее время часть труб с трубопрокатных заводов поступает с защитной консервацией. Для возможности выполнения последующих технологических операций требуется удалить эту консервацию. В зависимости от состава защитной смазки она удаляется или теплой водой, или уайт-спиритом, если в ее составе присутствуют масла. Такая промывка труб производится вручную. Удаление консервации может быть осуществлено путем обжига труб в печи или газовыми горелками.
Следующей операцией подготовки труб является сортировка труб по длине, диаметру и толщине стенки. Для рационального раскроя труб необходима их сортировка по длине, так как при поставке труб всегда имеется определенный процент немерных труб. Около 5% труб в партии отличаются по длине на 150-200 мм. Это дает возможность экономичного подбора труб согласно данным раскроя, так как отходы при резке в размер оказываются минимальными.
На котлостроительных заводах сортировку труб осуществляют на механизированных линиях, на которых сортировка по длинам осуществляется автоматически.
Внутри каждой партии целесообразна сортировка труб по фактическим толщинам стенок. Затраты на эту трудоемкую операцию окупаются повышением качества сварного соединения. Простейший способ сортировки такого рода основан на замерах труб контрольными калибрами.
После проведения всех подготовительных операций технолог цеха делает раскрой змеевика или трубы, т.е. определяет расположение сварных стыков на детали и в соответствии с этим количество и конфигурацию отдельных деталей, из которых в дальнейшем будет сварен змеевик или труба.
При составлении раскроя должны учитываться следующие требования:
1. Число сварных стыков должно быть наименьшим, а длина стыкуемых труб по возможности наибольшей. Поэтому желательно получить с трубопрокатных заводов трубы большей длины.
2. Запрещается располагать сварные стыки на гибах труб и в местах приварки к ним каких-либо деталей.
3. Сварные стыки должны быть доступны для ремонта на электростанциях.
4. От начала гиба до стыка должен быть прямой участок не менее 250 мм при контактной сварке и не менее 50 мм (но не менее диаметра трубы) при ручной сварке.
5. Раскрой должен обеспечить минимальные отходы труб.
6. При разработке процесса раскроя следует стремиться к возможно большему количеству одинаковых деталей (см. рис.).
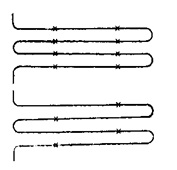
Котельные заводы определяют одно или несколько значений длин труб, которые удовлетворяют перечисленным выше требованиям, и заказывают мерные трубы именно таких длин.
Технолог при определении длины заготовки детали должен иметь ввиду, что трубы при гибке удлиняются.
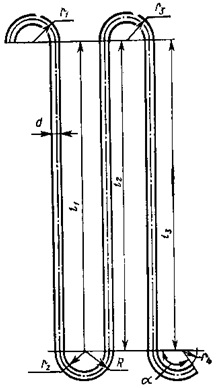
Развертка сложно-изогнутой трубы (змеевика) (см. рис.) подсчитывается по длине нейтральной линии, т.е. по оси трубы. Эта длина для змеевика на рис. Состоит из длин трех прямых участков l1+l2+l3, трех изогнутых на 180° участков и одного неполного, изогнутого на угол α участка. Длина развертки изогнутого участка равна S=(2πrα)/360, (при α=180°, S=πr). Определение развертки входит составной частью в операцию, называемую раскроем труб.
Раскрой производят следующим образом. На миллиметровой бумаге вычерчивают в виде прямой линии всю длину трубного элемента и отмечают на этой схеме положение сварных стыков, границ гибов и приварки деталей. Согласно полученной схеме раскроя определяют соответствующие длины труб и нумеруют заготовки порядковыми номерами. Длину труб назначают с учетом припуска под контактную сварку, т.е. учитывают, что в процессе оплавления труба укоротится. Длины трубных заготовок, подлежащих гибке, назначают с учетом вытяжки, тем самым учитывают, что заготовка в процессе операции гибки удлинится.
Таким образом, длина трубной заготовки отличается от длины трубы в составе трубного элемента на величину допуска под контактную сварку и на величину вытяжки при гибке. Длину трубной заготовки Lз, мм, определяют по следующей формуле:
Lз = Lр + δк + δв, где Lр развернутая длина по чертежу, δк – припуск под контактную сварку; δв – величина вытяжки.
За последние годы технология гибки труб усовершенствована настолько, что стало возможным производить их гибку без последующей обрезки концов трубы. Это позволило отказаться от операции резки гнутых труб и перейти на резку только прямых заготовок труб под гибку или контактную сварку.
Существует большое количество труборезных станков.
Оборудование для резки труб можно разделить на две большие группы:
1. Станки, при резке на которых обрезаемая труба вращается, а инструмент не имеет вращательного движения.
2. Станки, на которых труба при резке не вращается, а инструмент имеет вращательное движение с радиальной подачей.
Оборудование первой группы отличается шумом вращающейся трубы, быстрым износом при резке длинных труб даже с небольшой погнутостью, биением кривой трубы при вращении и связанной с этим опасностью для рабочего и окружающих.
Поэтому, безусловно, предпочтительнее оборудование, на котором труба при резке не вращается. Трудозатраты для второй группы станков на 3-5% меньше.
Обрезанные заготовки поступают на зачистку концов под контактную сварку в целях получения контактной поверхности, свободной от оксидов, механических и жировых загрязнений, обеспечивающей хороший электрический контакт трубы с губками сварочной машины. Длина зачистки зависит от конструкции губок контактно-сварочной машины и обычно составляет 200-250 мм.
Операция зачистки концов труб может быть выполнена несколькими способами:
1. Пескоструйной очисткой.
2. Зачисткой абразивными камнями.
3. Зачисткой иглофрезами.
4. Зачисткой непрерывной наждачной лентой.
5. Химической зачисткой.
В связи с появлением совершенных контактно-сварочных машин, оборудованных приборами для контроля качества сварки, требования к зачистке концов труб под сварку возросли: кроме зачистки снаружи на длине 250 мм, требуются зачистка внутренней поверхности трубы на длине 15-20 мм, а также зачистка торца трубы. Зачистка внутренней поверхности часто заменяется операцией зенкерования трубы.
Способы изготовления змеевиков и труб поверхностей нагрева
В котлостроении известно несколько различных способов изготовления элементов поверхностей нагрева.
Способ 1. Этот способ был преобладающим в 50-е годы. Предусматривалась резка заготовок труб, гибка всех деталей, зачистка их под сварку, сварка деталей в змеевик или трубу, плазировка, гидравлическое испытание и отделочные операции.

Гибка деталей была одной из первых операций, и все последующие операции (зачистка под сварку, сварка) производились на гнутых деталях.
Плаз представляет собой большую стальную или чугунную плиту, собранную из нескольких прямоугольных частей, соединенных на болтах. При изготовлении серии однотипных змеевиков применяют плазы, на которых вычерченный контур змеевика ограничивается по гибам и в средней части прямых участков вставленными в плаз гладкими штырями и для контроля контура целого змеевика после стыковой сварки.
Способ 2. Повышение параметров пара и применение в связи с этим высоколегированных труб для изготовления пароперегревателей вызвали необходимость разработки другого способа изготовления змеевиков, который первоначально использовался только при изготовлении змеевиков из нержавеющих сталей и стали 12Х2МФСР. При изготовлении змеевиков из этих сталей предыдущим способом, т.е. посредством контактной сварки заранее согнутых элементов, не удавалось удалить внутренний грат после сварки.

Поэтому начали сваривать между собой прямые заготовки в одну длинную плеть, и уже потом изгибать из нее змеевик, что позволило применить пневматический дорн с возвратно-поступательным движением для удаления внутреннего грата после сварки.
При такой «плетьевой» технологии операции резки, зачистки и сварки выполняют на прямых трубах, что позволяет их механизировать и даже автоматизировать (это «+»), но усложняется процесс гибки, так как приходится манипулировать с целым змеевиком и невозможна гибка с дорном («-«).
Ввиду явных преимуществ «плетьевой» технологии ее стали применять при изготовлении не только змеевиков из высоколегированных сталей, но и любых змеевиков и труб. На основе этой технологии разработаны механизированные линии изготовления змеевиков.
Изготовление змеевиков с использованием «плетьевой» технологии потребовало создания новых, специальных трубогибочных станков, исключающих кантовку змеевика при его гибке, поскольку гибка на обычных трубогибочных станках сопровождается многочисленными переворотами змеевика в процессе гибки.
Способ 3. В попытке использовать преимущества обоих рассмотренных способов был разработан третий способ изготовления змеевиков, при котором внутренний грат после сварки удаляется пневмодорном, а на гибке применяются обычные трубогибочные станки с использованием дорна и без кантовок змеевика.
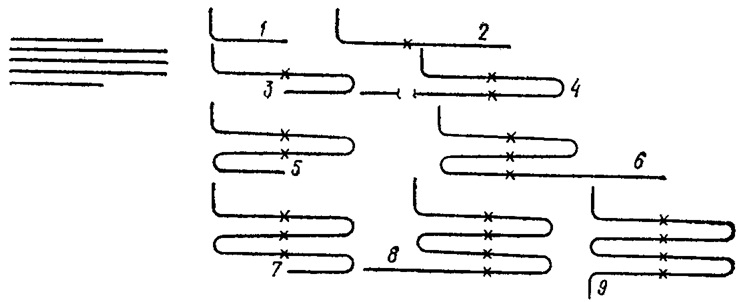
В этом случае изгибают первую деталь змеевика и сваривают с прямой заготовкой, следующей по раскрою детали. Внутренний грат удаляют со стороны прямой заготовки пневмодорном. После сварки обе детали поступают на трубогибочный станок, где их изгибают с пристыкованной заготовкой.
По окончании гибки и проверки качества гибов узел вновь поступает на контактно-сварочную машину, где к нему приваривают следующую прямую заготовку. Теперь на гибку подается узел из трех сваренных деталей и производится гибка приваренной прямой заготовки. Таким образом изготовляется весь змеевик.
Минусы. Недостатком этого способа являются частые перевозки змеевика в процессе изготовления и нерациональное использование гибочного и сварочного оборудования, которое простаивает во время перевозок и выполнения операций на соседнем рабочем месте. В связи с эти производительность труда при изготовлении змеевиков данным способом ниже, чем первых двух.
Изготовление водо-пароперепускных и других труб также можно вести двумя технологическими вариантами:
1. Гибка элементов трубы и последующая их сварка в целую трубу.
2. Сварка трубы заготовки в плеть и последующая ее гибка.
В первом варианте операция гибки не представляет сложностей, поскольку гибке, как правило подвергается труба длиной 6-9 м и можно использовать дорн. На операции сварки гнутых элементов трубы следует тщательно следить за правильностью разворота ее отдельных частей.
Во втором варианте проще операция сварки, так как свариваются прямые трубы, но сложнее операция гибки, поскольку исключена гибка с дорном и приходится кантовать трубу длиной 12-16 м.
Современному уровню технологии котлостроения отвечают следующие технологические маршруты изготовления трубных элементов поверхностей нагрева и водо-пароперепускных труб:
I. Технологический маршрут изготовления змеевиков и труб из согнутых элементов
1. Входной контроль труб. Проверка сертификатов, очистка труб по всей наружной поверхности, снятие колпачков, осмотр и обмер труб, УЗД, стилоскопирование.
2. Разметка и резка труб (при резке по упору разметка не производится).
3. Подготовка концов труб под контактную сварку. Зачистка внутренней поверхности трубы на 15-20 мм от торца трубы. Зачистка наружной поверхности трубы на 250-300 мм от торца, если не производилась очистка трубы по всей наружной поверхности. Эти операции могут быть выполнены и после гибки трубы.
4. Гибка труб и контроль согнутых элементов.
5. Контактная сварка элементов змеевика или трубы. Удаление внутреннего и наружного грата после сварки.
6. Плазировка змеевика или трубы.
7. Сборка и сварка приварных деталей. Стилоскопирование.
8. Гидравлическое испытание и прогонка контрольного шара.
9. Сборка змеевиков в пакеты.
10. Окраска, маркировка и упаковка пакетов змеевиков.
II. Технологический маршрут изготовления змеевиков и труб по «плетьевой» технологии
1. Входной контроль труб.
2. Разметка и резка труб.
3. Подготовка концов труб под контактную сварку.
4. Контактная сварка плети.
5. Гибка плети в змеевик.
6. Плазировка змеевика.
7. Сборка и сварка приварных деталей.
8. Гидравлическое испытание.
9. Сборка змеевиков в пакеты.
10. Окраска, маркировка и упаковка пакетов змеевиков.
Как видно из сравнения технологических маршрутов, большинство операций у них одинаковы. Разница состоит в операциях гибки и контактной
сварки. Кроме этого при «плетьевой» технологии отпадает операция контроля согнутых элементов змеевика или трубы, что сокращает трудозатраты на 5-8%.
III. Технологический маршрут изготовления водо- пароперепускных труб
1. Входной контроль труб.
2. Разметка и черновая резка труб (последняя выполняется газовой резкой или отрезными дисковыми пилами).
3. Чистовая обработка торцов труб.
4. Гибка труб.
5. Сборка и сварка приварных деталей.
6. Гидравлическое испытание труб.
7. Окраска, маркировка и упаковка труб.
Гибка труб
Гибка труб различных диаметров широко применяется в котлостроительной промышленности и наряду со сваркой является основной технологической операцией.
Ежегодно в отрасли производится несколько миллионов гибов.
Основное требование к гибке трубы заключается в сохранении неизменным проходного сечения в месте гиба.
Гибы труб при изготовлении котла очень разнообразны. Угол загиба трубы может достигать 360° (спиральный змеевик); между двумя соседними гибами может не быть прямого участка (гибка «из гиба в гиб»), причем такая гибка может выполняться как в одной плоскости, так и в разных плоскостях; прямые участки до и после гиба могут быть самой разной длины.
Что происходит с профилем трубы в процессе гибки?
При изгибе трубы в ее стенках возникают напряжения: снаружи растягивающие, внутри – сжимающие. Эти изменения вызывают:
— превращение круглого поперечного сечения трубы в овальное;
— уменьшение толщины стенки трубы на выпуклой стороне и увеличение на вогнутой;
— образование на вогнутой стороне складок (гофр).
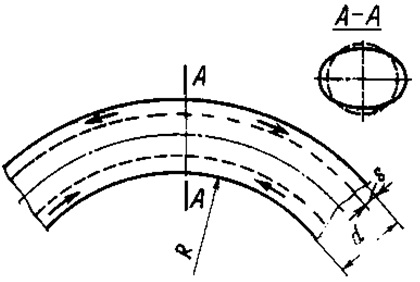
Следует иметь ввиду, что пластическая деформация при гибке распространяется на зону изгиба трубы и на прилегающие к ней прямые участки длиной около полутора- двух диаметров трубы; поэтому здесь также нарушается поперечное сечение трубы.
Овальность трубы в месте гиба в основном зависит от радиуса гиба и отношения толщины стенки трубы к ее диаметру. Большая ось овала поперечного сечения согнутого участка трубы располагается в плоскости, перпендикулярной плоскости изгиба. Степень овальности а выражается в процентах: a=(Dmax-Dmin)/Dн х 100% или
a=2(Dmax-Dmin)/(Dmax+Dmin) х100%
где Dmax – большая ось овала,
Dmin – малая ось овала,
Dн – диаметр трубы (номинальный).
Овальность не должна превышать 10% для труб поверхностей нагрева диаметром до 76 мм и 8% для соединительных труб и трубопроводов.
Овальность трубы в месте гиба уменьшает площадь поперечного сечения.
Вероятность появления гофр, как и овальности, увеличивается с уменьшением радиуса гиба и отношения толщины стенки трубы к ее диаметру. Гофры повышают сопротивление движению среды и являются очагами засорения и коррозии трубы.
Исходя из изложенного, желательно производить гибку труб на возможно больший радиус, применяя толстостенные трубы, так как при этом проще всего обеспечить качество гиба.
При гибке относительно тонкостенных труб на радиус гиба 3Dн и менее сечение трубы в месте гиба имеет недопустимый эллипс, а иногда, кроме этого, на внутренней стороне гиба появляются гофры. Для предотвращения подобных явлений гибка таких труб производится на специальной оправке, вставляемой на тяге внутрь трубы. Такая оправка называется дорном. Регулировкой дорна достигается нужное качество гиба.
Дорн представляет собой стержень с гибкими дисками, который находится внутри трубы. Гибка с дорном обеспечивает малый радиус гиба, гладкий ровный изгиб, минимальную овальность трубы в месте гиба.
Гибка труб может быть подразделена на станочную и ручную.
Ручная гибка ввиду низкой производительности в котлостроении практически не применяется.
Гибка на станках может быть вхолодную и вгорячую. «Горячая» гибка имеет меньшую производительности по сравнению с «холодной». При изготовлении станционных трубопроводов из труб большого диаметра с большой толщиной стенки, изгибаемых на малые радиусы применяется технология гибки труб с нагревом токами высокой частоты (ТВЧ).
Наибольшее распространение в котлостроении получила гибка труб вхолодную на станках. Этим способом гнут трубы диаметром до 219 мм, причем гибка может выполняться методами: наматывания и обкатки.
Рассмотрим гибку труб методом наматывания на сектор.
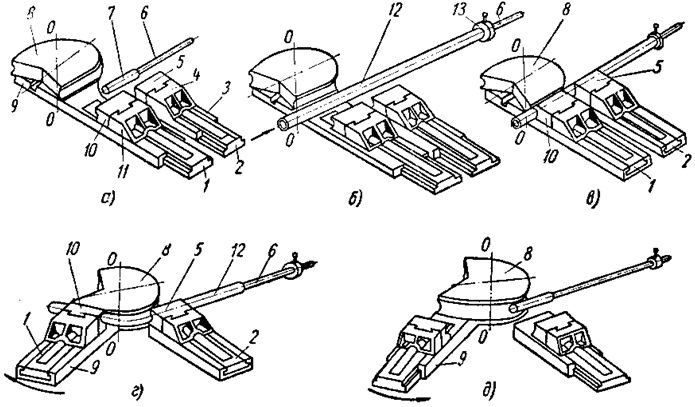
Цикл гибки труб на станке состоит из пяти основных приемов.
1-й прием заключается в подготовке рабочих органов станка к загрузке трубой.
Суппорты 1 и 2 вместе с упорами 11 и 4 и сменными вкладышами 5 и 10 отодвинуты от гибочного сектора 8. Сектор скреплен с поворотным столом 9 и располагается на общей с ним оси О-О.
Вкладыши, сменяемые в зависимости от диаметра труб, соединены с упорами 11 и 4 ласточкиным хвостом. Прижимной вкладыш 5 имеет гладкую поверхность желоба, по которому скользит труба. Зажимной вкладыш 10 имеет насечку на поверхности желоба для предупреждения выскальзывания трубы из зажима. Стержень 6 с дорном 7 отодвинуты вправо. Вторым концом стержень шарнирно соединен со штоком гидравлического цилиндра.
2-й прием заключается в загрузке станка трубой.
На стержне 6, после подачи стержня влево, в нужном месте устанавливается и закрепляется болтом фиксатор 13. Со стороны, указанной стрелкой, на дорн надевается труба 12, которая считается установленной, как только она достигает фиксатора.
3-й прием заключается в установке рабочих органов станка в положение, соответствующее началу гибки трубы. Свободный конец трубы зажимается между сектором 8 и зажимным вкладышем 10. Вкладыш 5 прижимает трубу к сектору, создавая направление и поддерживая трубу при гибке. Зажим конца трубы и прижим трубы к сектору осуществляются путем перемещения суппортов 1 и 2 в направлении сектора 8 под действием гидравлического давления.
4-й прием заключается в выполнении гибки трубы, т.е. в рабочем ходе станка.
В процессе рабочего хода станка труба 12 зажата между гибочным сектором 8 и суппортом 1 с зажимным вкладышем 10. Дорн находится при этом в зоне гиба. Стол 9 поворачивается вместе с гибочным сектором вокруг оси О-О с помощью гидравлического привода.
Труба 12, опираясь на неподвижный прижимной вкладыш 5 и скользя по нему, изгибается по форме гибочного сектора 8. Процесс изгибания трубы продолжается до тех пор, пока поворотный стол 9 с трубой 12 не повернется вокруг оси О-О на заданный угол и привод его автоматически выключится.
После отключения привода поворота стола и остановки станка рабочий с помощью гидравлического привода, связанного со стержнем, вытягивает дорн из зоны гиба трубы. Затем отодвигается прижимной суппорт 2 и труба снимается со станка.
5-й прием, завершающий цикл гибки трубы, заключается в возврате с помощью гидропривода поворотного стола 9 и гибочного сектора 8 в исходное положение.
На этом заканчивается цикл одного гиба трубы.
Гибка труб методом обкатки
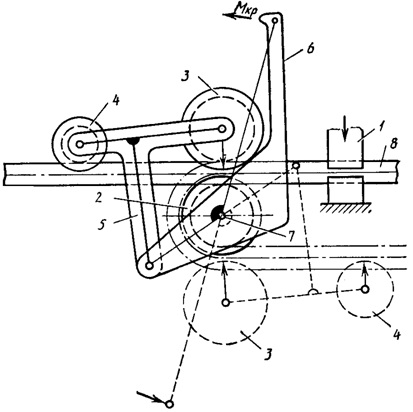
В последнее время все чаще внимание технологов привлекают трубогибочные станки с использованием метода обкатки, при котором гибочный сектор 2 в процессе гибки остается неподвижным, труба 8 крепится в зажиме 1 и также становится неподвижной. Участок трубы, который должен быть согнут, подвергается воздействию двух роликов: первый из них (по ходу гибки) 4 является изгибающим, второй 3 – калибрующим. Оба ролика заключены в единую обойму 5 и свободно вращаются на своих осях. Обойма с роликами прижимается к изгибаемой трубе и ей сообщается вращательное движение вокруг гибочного сектора. Гибочный сектор в различных конструкциях станков может быть установлен горизонтально либо вертикально. Применение дорна при гибке обкаткой выигрыша не дает, так как труба относительно дорна неподвижна и он не калибрует трубу в процессе гибки. Для уменьшения овальности трубы в данном случае служит калибрующий ролик, который движется по гибу трубы вслед за изгибающим роликом.
Таким образом, при гибке обкаткой возможна только бездорновая гибка, что ограничивает ее применение при гибке труб на малые радиусы гиба. Кроме этого, при гибке обкаткой на трубе до начала гиба должен быть оставлен достаточно большой прямой участок, иначе конец трубы не захватится изгибающим роликом. При гибке обкаткой невозможна гибка «из гиба в гиб», без прямого участка между соседними гибами. В этом отношении гибка труб методом наматывания более универсальна.
Гибка труб с индукционным подогревом
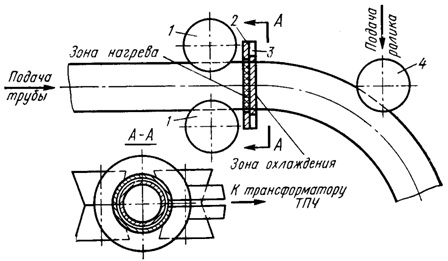
Этот способ гибки является одним из наиболее совершенных способов.
На трубе, подаваемой направляющими роликами 1, с помощью кольцевого индуктора 2 ТВЧ (токов высокой частоты) нагревают узкий участок трубы и изгибают его с помощью нажимного гибочного ролика 4. При этом нагретый участок пластически деформи-руется, в то время как близлежащие холодные зоны с относительно низкой пластичностью препятствуют образованию овальности. Для поддержания минимальной ширины нагретой зоны, труба на выходе индуктора интенсивно охлаждается водой кольцевым спрейером 3. Процесс гибки складывается из нескольких стадий: продвижение трубы под нажимной ролик; подвод нажимного ролика к трубе (начало гибки); взаимное перемещение трубы и нажимного ролика (труба перемещается в продольном направлении, а нажимной ролик – в поперечном) и гибка при неподвижном ролике и при перемещении только трубы.
При достижении заданного угла гиба механизм подачи останавливается, и процесс гибки прекращается. Радиус гиба зависит от конечного положения нажимного ролика и задается соответствующей настройкой оборудования. Угол гиба зависит от величины продвижения трубы.
Процесс гибки с нагревом ТВЧ эффективен при изготовлении трубных элементов с различными радиусами гиба и в различных плоскостях и находит применение в единичном и мелкосерийном производстве. Способ характерен меньшим утонением стенки и меньшей овальностью трубы, чем при других способах гибки.
Гибка труб на трубогибочных станках любой конструкции выполняется с помощью гибочной оснастки: гибочного шаблона (гибочной головки), прижимного устройства, направляющего корыта или роликов, изгибающего и калибрующего роликов, а также дорна. Гибочный шаблон, прижим, ролики, корыто имеют профилированный желоб, равный диаметру изгибаемой трубы.
Гибка может производиться по разметке или по упору, устанавливаемому на станине станка. В случае гибки по разметке на трубе мелом наносят риски, соответствующие местам гиба и прямых участков. При разметке длина изгибаемого участка корректируется с учетом вытяжки труб при гибке. Гибка по упору предпочтительнее, так как отпадает операция разметки труб и связанные с ней ошибки; кроме того, повышается производительность труда.
При проектировании трубного изогнутого элемента утонение трубы в гибе учитывают выбором большей, чем расчетная, толщины стенки трубы (определяется нормами расчета на прочность). В чертеже обычно указывают угол и радиус гиба.
Сварка труб
Основным видом сварки при изготовлении змеевиков водяного экономайзера, пароперегревателя и труб экрана является контактная сварка на специальных контактно-сварочных машинах.
Метод контактной сварки наиболее производителен в условиях массового производства однотипных деталей.
Особенность контактной сварки – отсутствие контроля качества сварных соединений существующими в настоящее время неразрушающими методами контроля.
Поэтому основным средством обеспечения высокого качества сварки является оснащение сварочных машин регистрирующими устройствам, контролирующими параметры сварки каждого стыка и обеспечивающими постоянство сварочных параметров. В целях контроля качества сварки предусматривается систематическое испытание экспресс-образцов.
Контактная сварка стыков освоена для всех марок котельных сталей. Из других видов сварки применяется полуавтоматическая многослойная сварка под слоем флюса для сварки водо-пароперепускных труб диаметром 133 мм, и ручную сварку, с помощью которой привариваются различные мелкие детали на змеевиках и трубах, развилки экранов. Иногда ручной сваркой выполняются стыки опускных и пароперепускных труб. Особым видом сварки является приварка шипов на экранных трубах.
Контактная сварка является одним из способов сварки давлением. Осуществляется она с местным нагревом и сжатием благодаря выделению теплоты, возникшей в месте повышенного сопротивления при прохождении электрического тока через цепь, в которую включены свариваемые детали. контакт между этими деталями создается в том месте, где они должны быть сварены между собой. Сопротивление контакта прохождению тока значительно больше, чем сопротивление сплошного металла. Это обстоятельство влечет за собой усиленное местное выделение теплоты на участке соприкосновения деталей, что как раз и необходимо для сварки, металл в зоне сварки нагревается до пластического состояния, и концы труб сжимаются под действием давления, прикладываемого на свариваемом участке.
Различают два вида стыков контактной сварки: сварку сопротивлением и сварку оплавлением.
При сварке сопротивлением детали вначале сжимают, а затем к ним подводят электрический ток и соединяемые концы труб нагревают до пластического состояния, после чего ток выключают и одновременно с этим производят осадку (в настоящее время этот вид сварки не применяется ввиду возможного брака стыков).
Широко применяется стыковая сварка непрерывным оплавлением. В этом случае ток включают до соприкосновения труб. При очень слабом давлении вначале медленно, а затем быстрее трубы сближают. В момент их соприкосновения на свариваемых поверхностях в точках касания возникает интенсивное искрение, металл на торцах труб оплавляется. После этого трубы подвергают осадке.
Осадка разогретых концов свариваемых труб необходима для удаления из плоскости контакта разогретого наружного слоя уже окисленного воздухом металла и его окалины. При осадке в соприкосновение вступают глубинные разогретые, но неокисленные слои металла, поскольку к ним не было доступа воздуха. Окисленный металл выдавливается вовнутрь и наружу стыка, образуя грат. Осадка необходима также для того, чтобы вступили в действие силы молекулярного сцепления свариваемых концов труб. При выполнении этих условий обеспечивается надежное соединение труб.
В связи с отсутствием неразрушающих методов контроля сварных швов, выполненных контактной сваркой, требуется оснащение контактно-сварочных машин приборами автоматического контроля основных параметров процесса сварки.
Перед началом сварки сварщик устанавливает в зажимы машины медные губки, соответствующие диаметру свариваемых труб, затем проверяет центровку зажимов. Эту операцию он выполняет с помощью контрольных валиков, которые зажимают в губки машины.
Сварка начинается с укладки одной из свариваемых труб и зажатия ее в губках машины. Трубу укладывают в губки так, чтобы вылет ее конца из губок составлял половину расстояния между зажимами. В другой зажим помещают вторую свариваемую трубу так, чтобы ее торец соприкасался с торцом первой трубы. На одну из свариваемых деталей одевают наконечник, подводящий кислородно-воздушную смесь при кислородной продувке для удаления внутреннего грата, или наконечник воздушного шланга, с помощью которого прогоняют шар или снаряд для удаления внутреннего грата. При сварке прямых труб в этот конец для удаления внутреннего грата заводят пневматический дорн. На свободный конец другой свариваемой детали устанавливают ловушку для искр или шароуловитель.
Внутренний грат в трубах может быть удален несколькими способами. Наиболее употребительными являются способы удаление внутреннего грата:
• пневматическим дорном;
• шаром;
• снарядом;
• воздушно-кислородной смесью.
В процессе контактной сварки внутренняя поверхность трубы в месте сварного стыка загрязняется брызгами металла, которые не поддаются удалению ни одним из способов удаления внутреннего грата. Для уменьшения образования этих брызг перед сваркой в концы труб укладывают картонные кольца, которые защищают внутреннюю поверхность труб. Ширина кольца примерно 20-30 мм. После сварки кольцо удаляется из трубы в процессе удаления внутреннего грата.
Удаление грата кислородно-воздушной смесью основано на свойстве стали гореть в среде кислорода. При сварке труб из высоколегированных сталей внутренний грат кислородом не удаляется, так как он не горит в кислороде.
Время продувки составляет 1-1,5 с. Причем смесь подают через 0,2-0,3 с после осадки. При большем интервале времени температура грата может стать ниже температуры воспламенения стали и грат не будет удален.
После продувки остается некоторое количество окалины, которую удаляют прогонкой шара. При любом количестве стыков шар прогоняется только один раз, после сварки последнего стыка. Этот шар является одновременно и контрольным. Его диаметр 0,8-0,86 внутреннего размера трубы.