Изготовление барабанов (продолжение)
Первая часть изготовления барабана описана тут.
Откалиброванные и очищенные от окалины полуобечайки с обработанными продольными кромками поступают на сборочный стенд, который представляет собой раму с установленными на ней несколькими парами катков. Для сборки подбирают полуобечайки с минимальным расхождением по диаметру.
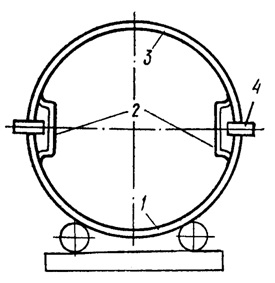
Сборку начинают с установки на кантователь нижней полуобечайки 1 кромками вверх. На обе кромки этой полуобечайки укладывают по 2-3 дистанционные пластины 4, обеспечивающие необходимый зазор для сварки. Пластины имеют размер 250-100 мм и толщину, равную зазору под сварку. По краям пластины имеют отверстия, в которые можно вставить клин и, при необходимости, немного сдвинуть укладываемую сверху полуобечайку 3 относительно нижней для выравнивания перепада по продольным кромкам. Вторая полуобечайка перекантовывается с помощью мостового крана кромками вниз и укладывается на первую обечайку через дистанционные пластины. При сборке проверяется угловатость в месте продольного стыка, она замеряется шаблоном и не должна быть более 3-5 мм в зависимости от диаметра барабана. Здесь же проверяется диаметр собранной обечайки.
Уложенные одна на другую полуобечайки соединяют между собой малыми технологическими скобами 2. Эти скобы вырезают из листа толщиной 40-50 мм и привариваются по одной к технологическим выступам обечайки (крайним).
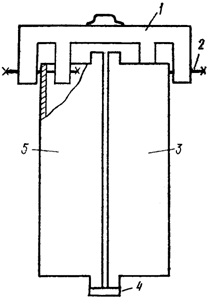
В верхней части обечайки, по оси, расположенной перпендикулярно оси сварных швов, устанавливают большую технологическую скобу 1 крепящуюся на средних технологических выступах полуобечаек 3 и 5 с помощью винтов 2 диаметром 100-130 мм с трапецеидальной резьбой. Эта скоба, как и малые сборочные скобы, предотвращает развал обечайки при транспортировке и сварке. Внизу на торцы технологических выступов обечайки устанавливают и приваривают две крепежные планки 4 толщиной 30-50 мм.
Особое внимание при сборке обращают на смещение кромок и зазор между полуобечайками под сварку.
В случае большого смещения ползун сварочного аппарата не плотно прилегает к поверхности обечайки, и возможно вытекание шлаковой ванны. По этой же причине кромки полуобечаек тщательно зачищают от местных зарубок, выбоин, вмятин и т.п. При необходимости эти местные дефекты подвариваются и зачищаются шлифмашинкой. Зачистка производится на величину 60 мм от кромки. Перепад (смещение) кромок и местные дефекты не должны быть более 3 мм.
Зазор между кромками определяется методом сварки и толщиной листа. При многослойной сварке под слоем флюса он составляет величину 0,5-1 мм, для электрошлаковой сварки 25-34 мм.
Зазор между двумя полуобечайками, собранными для ЭШС выполняется неравномерным. Внизу собранной обечайки (начало сварки) он на несколько миллиметров больше, чем сверху обечайки (конец сварки). «Клиновой» зазор необходим потому, что, несмотря на приваренные технологические сборочные скобы, в процессе сварки происходит деформация обечайки и зазор вверху обечайки увеличивается до недопустимых пределов. «Клиновый» зазор при сборке обеспечивает равномерный зазор при сварке по всей длине сварного шва. Этот технологический прием применяют при сварке обечаек с толщиной стенки более 70 мм. При меньших толщинах стенки обечайки напряжения при сварке не столь велики, чтобы существенно повлиять на величину зазора.
Транспортируют собранную обечайку на сварку с помощью крана, зацепив обечайку за большую технологическую скобу, которая для этой цели имеет специальное «ухо».
В настоящее время основными способами сварки продольных и поперечных швов цилиндрических частей сосудов является автоматическая сварка под слоем флюса с автоматической подваркой корня шва (АСФ) и автоматическая электрошлаковая сварка (ЭШС).
Сварка под флюсом (плюсы и минусы)
Преимущества (по сравнению с ручной) | Недостатки |
производительность выше в 5-20 раз; | можно выполнять только в нижнем положении из-за высокой текучести сварочной ванны |
сварные швы отличаются высокой стабильностью качества, за счет хорошей защиты металла сварочной ванны от воздействия кислорода и азота воздуха, очищающего действия шлака; | |
экономия сварочных материалов, так как производство проволоки и флюса дешевле, чем производство штучных электродов полная автоматизация процесса сварки, отсутствие светового излучения, меньшая загазованность окружающего пространства; | |
не требует оператора- сварщика высокой квалификации; |
Электрошлаковая сварка
Преимущества | Недостатки |
возможность сварки металла практически любой толщины за один проход; | возможность сварки только в вертикальном положении; |
отсутствие необходимости в операции подготовки разделки кромок; | необходимость проведения высокотемпературной термической обработки сварных изделий, особенно из легированных сталей большой толщины; |
малая вероятность образования трещин и пор; | недопустимость остановки процесса (если по какой-либо причине процесс сварки прерывается, то образующийся дефект удалить практически невозможно; |
незначительный расход флюса, всего 2-5% от массы наплавленного металла; | сложность сборки деталей под сварку, стык собирают с применением технологических деталей в виде планок, стартовых карманов, формирующих устройств |
небольшой расход электроэнергии, примерно в 2 раза меньше чем при сварке под флюсом; | |
более высокая производительность, чем у других способов сварки |
Установка для многослойной сварки внутренних или наружных швов состоит из сварочного автомата и роликового стола или кантователя для перемещения обечайки.
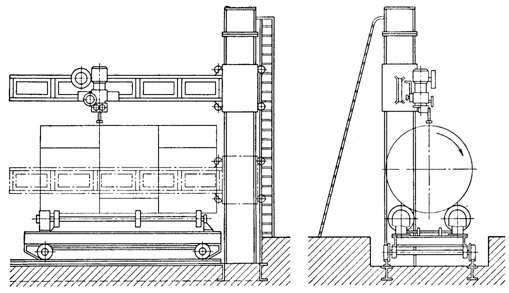
При сварке кольцевых швов сварочная головка неподвижна, а вращается на кантователе обечайка. При сварке продольных швов обычно (технология принятая на ТКЗ, БКЗ) обечайка остается неподвижной, а сварочная головка двигается вдоль шва со скоростью сварки.
Для сварки требуется определенная разделка кромок швов, которая производится:
— для тонкостенной обечайки на заготовке в листе;
— для толстостенных сосудов на корыте или обечайке.
После сварки продольных швов ЭШС обечайку необходимо подвергнуть термообработке для разрушения крупных зерен в структуре наплавленного металла. Для этого проводят нормализацию.
При многослойной сварке под слоем флюса нормализация сварных швов не требуется, так как структура шва оказывается мелкозернистой.
Форма обечайки после сварки часто отклоняется от правильной цилиндрической. Для придания обечайкам цилиндрической формы их подвергают калибровке путем обкатки на листогибочных вальцах. Калибровка производится как в горячем, так и в холодном состоянии. Обечайки из углеродистой стали со стенками толщиной 25 мм и более и из легированной толщиной 10 мм и более подвергаются калибровке в горячем состоянии. Температурный интервал такой же как при горячей вальцовке. После окончания процесса калибровки обечайка свободно вращается в вальцах до потемнения (500-600 С), после чего снимается краном и охлаждается на воздухе. Нагрев обечайки под калибровку служит одновременно и нагревом для нормализации, в процессе которой сварные швы и околошовная зона освобождаются от сварочных напряжений.
Для ультразвукового контроля продольных швов обечаек на них шлифовальной машинкой зачищают вдоль сварного шва с обеих сторон полосы шириной 60 мм внутри и снаружи обечайки. По ним перемещают ультразвуковые датчики при контроле швов. Места с дефектами в сварных швах ремонтируют.
Перед обработкой торцов обечайки под сварку кольцевых швов, излишний припуск на торцах обрезают газовой резкой вручную или на специальных установках.
Стационарная установка для обрезки газом торцевых кромок обечайки состоит из механизированного роликового конвейера, на который укладывают обечайку, и портала с находящейся на нем газорезательной аппаратурой. Портал может передвигаться вдоль конвейер. В процессе резки обечайка вращается с заданной скоростью на конвейере. Обрезку газом в данном случае применяют как черновую.
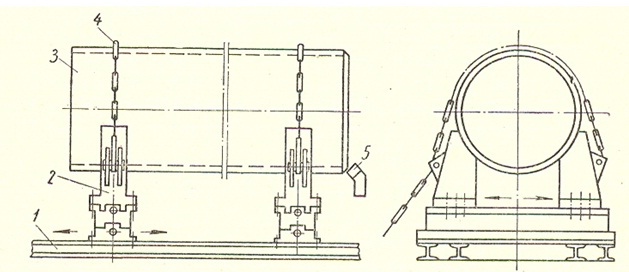
1 – рельсовый настил; 2 – опоры; 3 – барабан; 4 – зажимные цепи;
5 – резец.
Чистовую обработку торцов обечайки выполняют на кромкообточных или расточных станках. Эти станки позволяют обрабатывать торец обечайки под любой вид сварки.
Такая механическая обработка торцов и профиля обечайки необходима для точной сборки корпуса барабана и качественной сварки кольцевых швов. Обработанные обечайки поступают на сборку корпуса барабана.
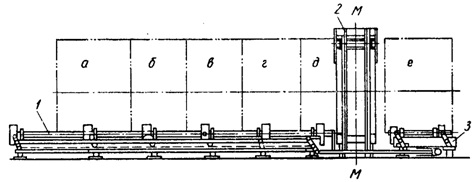
Конструкция стенда для сборки кольцевых стыков барабанов, в котором механизированный ролик (кантователь) сочетается с устройством для выравнивания стыкуемых кромок обечаек.
Порядок работы установки следующий: обечайку а устанавливают в начале кантователя 1 так, чтобы правая кольцевая кромка ее совместилась с осью ММ сборочного устройства 2. Затем на подающую тележку 3 укладывают обечайку б, после чего тележка, перемещаясь вдоль стенда, подает обечайку в сборочное устройство до соприкосновения ее с кромкой обечайки а. После этого включается в работу сборочное устройство 2, которое при помощи пневматических и гидравлических зажимов стягивает в радиальном направлении обе кромки стыкуемых обечаек, образуя нормальный стык под сварку. Собранный стык фиксируется приварными поперечными планками на внутренней поверхности обечайки. Затем собранные обечайки а и б перемещаются с помощью особого устройства вдоль стенда до тех пор, пока правая кольцевая кромка обечайки б не совместится с осью ММ сборочного устройства 2. На подающую тележку устанавливается следующая обечайка и процесс повторяется. После установки последней обечайки собранная цилиндрическая часть барабана передается на сварку кольцевых швов.
Описанный сборочный стенд целесообразно применять в серийном производстве при изготовлении однотипных барабанов, так как сборочное устройство стенда, являясь охватывающим, должно строиться для каждого типоразмера барабана отдельно, исходя из его диаметра.
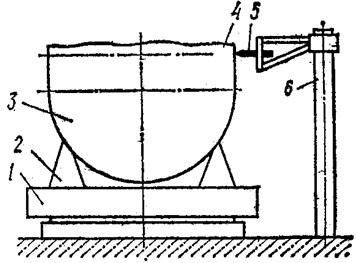
Днища после штамповки и очистки от окалины подают сначала на разметку под обрезку припуска по высоте кромки и вырезку лазового отверстия. Обрезку производят на карусельной газорезательной установке, на которой вырезают и лазовое отверстие. Установка состоит из поворотного стола 1 с упорами 2 для укладки и вращения днища 3 и колонны 6 с блоком газовых резаков 5, которая имеет механизмы вертикального и горизонтального перемещений блока резаков.
Подводка днищ к цилиндрической части барабана и выравнивание их кромок в кольцевом стыке может осуществляться различными способами.
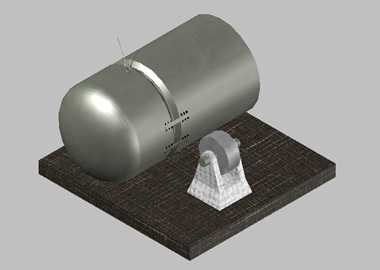
В мелкосерийном производстве, отличающемся большим разнообразием типоразмеров барабанов, наибольшее распространение получил способ подводки днища на кране и выравнивание кромок в стыке при помощи приварных болтов, натяжных скоб и др.
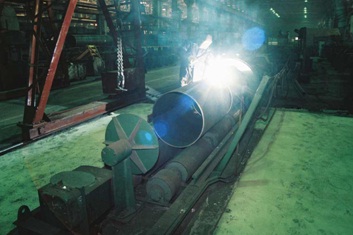
В серийном производстве с небольшим числом типоразмеров барабанов и сравнительно большой партией пуска их в производство целесообразно применять специальные приспособления, позволяющие сократить цикл сборки днища с корпусом.
Термообработка сосудов и контроль качества сварных швов
В результате сварки в сварных швах сосудов возникают внутренние напряжения вследствие усадки металла шва. Кольцевые швы охватывают более жесткий замкнутый контур, чем продольные, поэтому и сварочные напряжения в них выше. Снимают эти напряжения применением термической обработки – высокого отпуска. Согласно правилам Госгортехнадзора обязательной термообработке подлежат сосуды из углеродистой стали с толщиной стенки более 35 мм и из легированной перлитного класса с толщиной стенки 10 мм и более.
Если швы выполнены ЭШС то сначала сосуд подвергают нормализации, а после приварки штуцеров – высокому отпуску.
После нормализации производится обмер остывшего сосуда, а при необходимости калибровка. Отклонения по наружному диаметру не должны превышать 1%.
Для контроля качества сварных швов применяют УЗД, МПД, просвечивание рентгеновскими и гамма-лучами и др. Эти испытания проводят с целью определения сплошности металла, т.е. выявления непроваров, шлаковых включений, пор и трещин.
Контролю УЗД подлежат 100% сварных сосудов из углеродистой и легированной стали перлитного класса. При обнаружении сомнительных мест проводится проверка рентгено-дефектоскопией.
Для обнаружения поверхностных трещин 100% швов контролируется МПД.
Выполнение отверстий и установка штуцеров
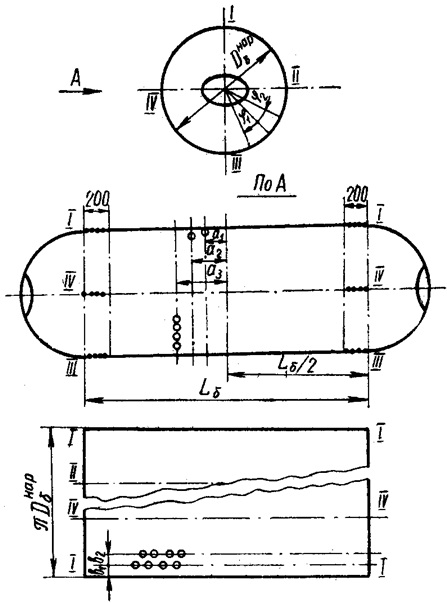
После приварки днищ, термообработки и контроля сварных швов барабан подается на стенд разметки отверстий под штуцеры.
На чертеже каждого котельного барабана выполняется развертка его наружной поверхности. На развертке нанесены продольные центровые линии (I-IV), делящие наружную окружность барабана на четыре равные части, и поперечная центровая линия А-А, делящая цилиндрическую часть барабана пополам. Эти центровые линии являются главными (базовыми). К ним привязываются центры всех отверстий. В соответствии с чертежом наносятся на барабан поперечные и продольные центровые линии – расцентровка барабана. Центровые линии барабана должны являться продолжением осей лазовых отверстий. Концы осевых линий накерниваются на длине 200мм на цилиндрической части барабана. Разметка отверстий производится в поперечном направлении – по дуговым размерам от главных продольных осей, а в продольном направлении – от середины цилиндрической части. В случае отклонения наружного диаметра от номинала все дуговые размеры подлежат перерасчету по фактическому размеру с сохранением значений углов альфа по чертежу. Центр отверстия накернивается и вокруг него диаметром равным диаметру отверстия по чертежу, проводится окружность, которая накернивается.
После разметки всех отверстий барабан поступает на приемку ОТК и далее на сверловку отверстий.
Сверловка отверстий производится на радиально-сверлильных станках. Для поворота барабана при сверловке отверстий он устанавливается на роликовых кантователях с ручным или механическим приводом.
Трубные отверстия выполняются по рядам в следующем порядке:
— зацентровка отверстий;
— сверловка;
— рассверловка отверстий с оставлением припуска на зенкерование.
Зацентровка служит для создания направления сверлу большого диаметра в начале и тем самым для сохранения центра отверстия в заданном чертежом месте. Зацентровка отверстий производится спиральным сверлом диаметром 12-15 мм на глубину 8-10 мм.
Далее производится сверловка сквозного отверстия на проход спиральным сверлом диаметром до 50 мм.
Рассверловка трубных отверстий до размера под развертку выполняется специальными зенкерами, изготавливаемыми диаметром от 50 до 120 мм.
Сверловка и рассверловка выполняется при обильном охлаждении эмульсией.
Отверстия диаметром более 120 мм могут обрабатываться по несколько иной технологической схеме. Предварительно газовым резаком вырезается отверстие с припуском 10 мм на сторону для дальнейшей обработки. Удаление припуска и доведение диаметра отверстия до номинального производится на расточном или радиально-сверлильном станке. Инструментом для расточки отверстий служит резец на оправке, установленной в шпинделе станка.
В настоящее время на котлостроительных заводах для сверловки отверстий в барабанах и коллекторах используются автоматические многошпиндельные (до 7 шпинделей) сверлильные станки с программным управлением. В этом случае размечается и накернивается только первый ряд отверстий. Отверстия сверлятся за один проход двухступенчатым сверлом, в верхней части которого имеется заточка под зенкер.
Зенкерование, способ обработки поверхностей отверстий, предварительно просверлённых, полученных горячей или холодной штамповкой и литьём. Зенкерование применяют при обработке цилиндрических отверстий, углублений под головки или шейки болтов и винтов, торцевых поверхностей бобышек под шайбы, упорные кольца. Повышает точность и чистоту поверхности, т.к.зенкер в отличие от сверла, имеет больше режущих кромок. Отверстие, полученное зенкерованием, имеет более точное по сравнению со сверлёным направление оси, поэтому зенкерование широко применяют при чистовой и получистовой обработке. Выполняется на сверлильных, револьверных и расточных станках.
Обработанные отверстия подвергают тщательному осмотру и контролю размеров калибрами. С наружной и внутренней сторон барабана отверстия очищают от заусенцев при помощи переносных пневматических шлифовально-зачистных машинок. Затем в отверстия устанавливают штуцера.
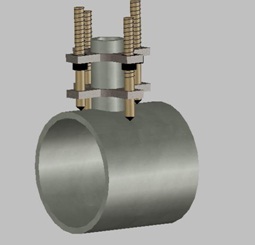
Установка и приварка штуцеров должны обеспечить правильное положение их на барабане или коллекторе.
Правильно установленный и проверенный щтуцер сначала прихватывается в нескольких местах электросваркой, а затем, после контроля его положения, привариваются.
Для приварки штуцеров диаметром до 133 мм применяются автоматические установки различной конструкции. Они состоят из роликовой постели, на которую укладывается барабан, и сварочной головки, которая оборудована двумя электродами и передвигается вдоль неподвижного барабана. Сварка производится под слоем флюса путем вращения электродов вокруг штуцера. Головка во время вращения надежно центрируется по оси штуцера.
Приварка всех щтуцеров к сосудам из легированной стали производится с предварительным подогревом зон сварки до 200-250 С газовыми горелками.
Одновременно с приваркой штуцеров сваривают контрольные образцы с применением тех же исходных материалов, и методов сварки. На каждые 200 приваренных штуцеров выполняется один контрольный образец, который вместе с сосудом проходит с барабаном проходит термообработку и затем образец подвергается металлографическим испытаниям.
Во избежание подгоночных работ при монтаже введены жесткие требования к сборке штуцеров. При контроле следят за тем, чтобы максимальное отклонение, измеренное между струной, натянутой по оси крайних штуцеров, и осью каждого штуцера данного ряда, не выходило за пределы 3 мм, чтобы перекос оси штуцера был не менее 1 мм.
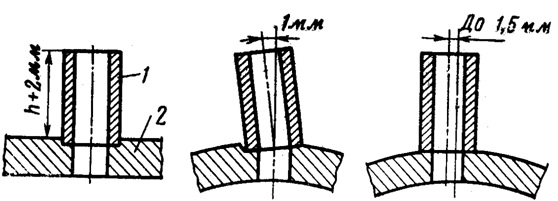
Контроль качества приварки штуцеров к барабану осуществляется внешним осмотром, гидроиспытанием, МПД, УЗД для диаметра 133 мм и выше ренгенопросвечиванием. При обнаружении в шве трещины или непровара штуцер диаметром до 108 мм удаляют, а штуцер диаметром более 108 мм удаляют, если более 1/3 шва дефектны. В остальных случаях дефектное место вырубают и заваривают вновь.
Гидравлическое испытание
Гидравлическое испытание барабана внутренним давлением, равным 1,25 рабочего давления, производится с целью проверки сварных швов на плотность. Перед проведением гидравлического испытания лазовые отверстия закрываются постоянными лазовыми затворами, имеющиеся на барабане штуцеры с фланцами заглушаются с помощью плоских заглушек, а штуцеры без фланцев приваркой плоских заглушек, удаляемых после окончания гидравлического испытания газовой резкой.
Место проведения испытаний должно быть надежно изолировано от остальных рабочих мест цеха, а внутри самого испытательного стенда необходимо предусмотреть защитные устройства для обслуживающего персонала.
Приварка заглушек к нескольким сотням штуцеров на барабане представляет собой трудоемкую и длительную операцию, в результате которой появляется большое количество отходов.
Более экономичным было бы заглушать штуцеры с помощью заглушек, вставляемых внутрь штуцера или одеваемых снаружи. Однако съемные заглушки пока еще недостаточно безопасны, что препятствует их широкому применению на котлостроительных заводах. В некоторых случаяхконцы штуцеров «окуполиваются», т.е. конец штуцера обжимается вгорячую, чем достигается необходимая плотность. При этом способе так же как и при приварке заглушек, велики отходы металла, и необходима неудобная операция – обработка кромок штуцеров под сварку.
Если обнаружен дефект сварного шва, то дефектное место вырубается пневматическим зубилом или выдувается газовой резкой на всю глубину и вновь заваривается. При ремонте применяются все виды сварки. После этого вновь повторяют дефектоскопию и гидравлическое испытание. Вырубка и заварка швов разрешается только в разгерметизированном барабане и при слитой из него воде. Это требование является одним из важнейших требований техники безопасности.
Монтаж внутрибарабанных устройств и подготовка его к отправке
После окончания гидравлического испытания для ускорения просушки барабана производят продувку его внутренней поверхности сжатым воздухом. Далее барабан поступает на разметку концов штуцеров под обрезку временных, заранее приваренных заглушек. После обрезки штуцеров газокислородным резаком барабан устанавливают под радиально-сверлильным станком для обработки фаски на торцах штуцеров под сварку. Дальнейшей операцией является установка в барабане его внутренних устройств, если они предусмотрены конструкцией.
При выполнении этих работ необходимо тщательно соблюдать требования техники безопасности – обязательно присутствие наблюдателя, находящегося вне барабана.
Внутрибарабанные устройства состоят из деталей, разделяющихся по способу крепления их в барабане на два основных вида:
— приварные (к барабану);
— устанавливаемые на болтовых соединениях.
Обычно приварные детали имеют отверстия под болты и несут не себе внутрибарабанное устройство.
Процесс сборки барабана с сепарационным устройством состоит из двух основных этапов:
— сборки и сварки с барабаном приварных деталей;
-контрольной сборки в барабане деталей внутреннего устройства на болтах.
По специальному чертежу, представляющему схему расположения приварных деталей в барабане, производится сначала расцентровка, т.е. нанесение продольных и поперечных осей на внутренней поверхности барабана, а затем разметка всех мест под установку и приварку деталей к барабану, исходя из осевых линий.
Примерная схема расположения приварных деталей внутрибарабанного устройства приведена на рисунке.
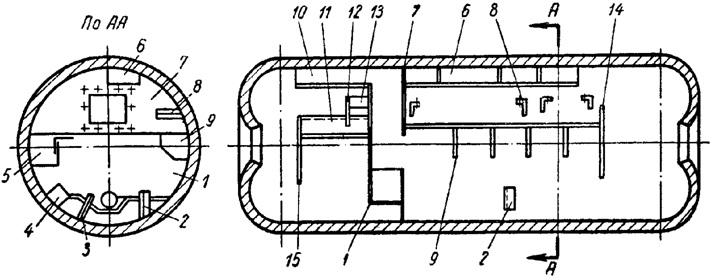
На схеме: 1 – перегородка между отсеками; 2 и 3 – угольники; 4 – колпак; 5 — кронштейн; 6 — верхний щит; 7 – перегородка; 8 – угольник; 9 – кронштейн; 10 – угольник из листа; 11 – щит; 12 — косынка; 13 – козырек; 14 – щит;15 – кронштейн.
На размеченные места устанавливаются детали и, в зависимости от того, где осуществляется окончательная приварка этих деталей – на заводе или при монтаже котла производится соответственно приварка к барабану сплошным электросварным швом или только прихватка электроточками. Прихваченные детали привариваются на монтаже после окончательной сборки внутрибарабанного устройства в барабане на паронитовых прокладках.
После приварки деталей сварные швы очищают от шлака и брызг пневматическими инструментами и шлифовальными машинками. Остальные детали внутрибарабанного устройства, устанавливаемые на болтовых или сварных соединениях, собирают перед размещением их в барабане в отдельные узлы на сборочном плазу вне барабана.
Габаритные размеры этих узлов не должны превышать размеров лазового отверстия в днище барабана, через которое их заводят в барабан.
Узлы с габаритными размерами больше этого отверстия заводятся в барабан в виде отдельных деталей, сборка которых в узлы производится внутри барабана.
После установки внутренних деталей в барабане лазы в днищах закрывают затворами.
Готовый барабан маркируют и снабжают табличкой установленной формы. На барабане и табличке выбивают необходимые паспортные данные.
Для защиты внутреннего объема барабана от влаги, загрязнений и попадания посторонних предметов все его отверстия на время транспортировки закрывают заглушками.
Чтобы предотвратить коррозию металла, обработанные механическим способом поверхности консервируют специальными консистентными смазками, а наружную поверхность барабана окрашивают краской, защищающей его от атмосферных воздействий в течение года.