Изготовление поверхностей нагрева – часть 2
Первая часть была рассмотрена изготовления поверхностей нагрева тут.
Плазировка
Проверка отдельных согнутых элементов и контроль изготовленного змеевика или трубы по рисунку, нанесенному на плаз, или по кондуктору с необходимыми подгоночными работами называется плазировкой. Для выполнения этой операции в цехе имеется несколько плазов, т.е. специальных мест, выложенных чугунными и стальными плитами, на которых в натуральную величину вычерчивается контур проверяемой детали. Плаз должен быть ровным, неплоскостность его отдельных участков должна быть не более 2 мм. Плазы обычно устанавливают вблизи гибочных станков, чтобы избежать лишних перевозок труб.
Подгонку детали при ее отклонении от чертежных размеров производят или вхолодную на станке для гибки труб, или вгорячую вручную на плазе. Подгонка в большинстве случаев заключается в подгибке либо разгибке гибов трубы. Для этой цели нагревают газовой горелкой место в непосредственной близости от гиба и, заложив в конец трубы ломик, подгибают или разгибают трубу.
В случае плазировки большой партии однотипных деталей целесообразнее производить плазировку не на плазу, а в специально изготовленном для этой цели кондукторе.
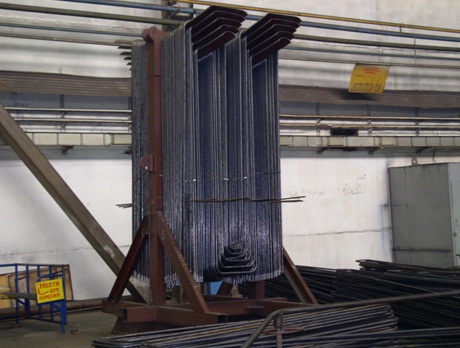
Кондуктор – представляет собой лист металла, на котором размечены контуры проверяемой детали и закреплено необходимое количество ограничителей, изготовленных из обрезков труб или листа толщиной 10 – 16 мм. После выполнения плазировки детали ограничители удаляют с листа кондуктора пневмозубилом, места их установки тщательно зачищают шлифовальной машиной, и кондуктор снова готов для разметки и установки ограничителей для плазировки следующей детали. Точность контроля в кондукторе выше, чем на плазе, т.к. кондуктор позволяет не вычерчивать контуры детали на плазе, что устраняет определенные ошибки.
Полностью сваренный на контактно-сварочной машине змеевик подвергается обязательной проверке на плазе или по кондуктору. Как правило, змеевики изготовляют достаточно большими партиями; поэтому для контроля чаще применяют кондукторы.
Очень важно проверить первый сваренный змеевик, иначе вся партия может быть сварена неправильно.
Часто изготовленный змеевик не полностью соответствует вычерченному на плазе или кондуктору. В таком случае производят подгонку змеевика до нужных размеров, причем змеевики из аустенитных сталей подгоняют только вхолодную, так как нагрев их газовой горелкой отрицательно сказывается на свойствах аустенитной стали.
Неприлегание змеевика к плоскости плаза или кондуктора не должно превышать 5 мм. Наиболее точно должны быть подогнаны концы змеевика (выходы), которыми он присоединяется к камере соответствующего блока котла.
Если при плазировке змеевиков и их деталей чаще применяются кондукторы, то при плазировке труб экрана, водоопускных и пароперепускных труб почти всегда пользуются плазом, что определено небольшим количеством однотипных труб.
Некоторые трубы экрана имеют большое количество приваренных шипов, в процессе приварки которых трубы сильно деформируются; поэтому выправить их вручную чрезвычайно трудно и с этой целью применяют небольшие прессы.
Изготовление цельносварных панелей
Существует четыре наиболее распространенных способа изготовления газоплотных панелей.
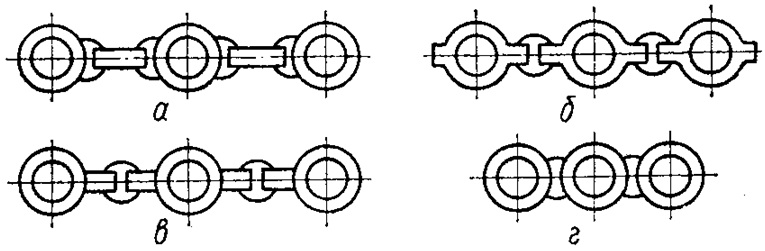
а) Из гладких труб с варкой между ними полосы-проставки.
б) Из плавниковых труб металлургического производства.
в) Из гладких, предварительно оребренных труб.
г) Из гладких труб с наплавкой между ними перемычки.
Панели изготавливают из труб диаметром 28-60 мм с минимальной толщиной стенки 4-5 мм. Размеры панелей обычно не превышают 24 м по длине и 3 м по ширине.
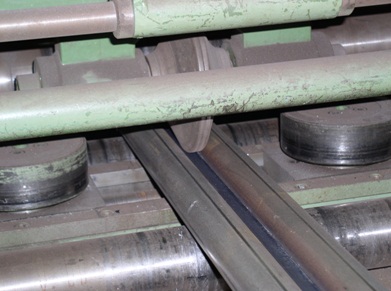
При существующем уровне технологии изготовления газоплотных панелей наиболее дорогостоящим является их выполнение из плавниковых труб металлургического производства. Дешевле изготовление панелей из гладких труб с заранее приваренными плавниками и еще дешевле их производство путем варки полосы между трубами. Большая стоимость газоплотных панелей из плавниковых труб металлургического производства определяется стоимостью самих труб, но объем сварочных работ при этом минимальный. Длина сварных швов в два раза меньше, чем в панелях из гладких труб с ввареной полосой между трубами, и в три раза меньше, чем в панелях из гладких, предварительно оребренных труб.
При изготовлении панелей применяют сварочные установки двух типов:
проходные и портальные. Различные модификации их позволяют сваривать между собой плавниковые или оребренные трубы, вваривать полосу между трубами, заполнять межтрубное пространство наплавленным металлом, образуя панель. Имеются установки с несколькими автоматическими сварочными головками, позволяющими выполнять сварку одновременно нескольких труб. Количество сварочных головок на установках проходного типа достигает 7 шт., т.е. одновременно можно сваривать восемь труб. На установках портального типа размещают до 5 сварочных головок. Как правило, производится сварка под флюсом.
Сварочные установки проходного типа позволяют сваривать панели шириной не более 1,6 м, а портальные обеспечивают сварку панелей до 3 м.
Сварочная установка проходного типа представляет собой П-образную конструкцию. На верхней поперечной траверсе станины устанавливают сварочные головки, которые могут перемещаться поперек станины и в вертикальном направлении. Свариваемые трубы перемещаются в продольном направлении по приводным горизонтальным роликам, к которым они прижимаются до и после места сварки верхними нажимными роликами. Эти ролики обеспечивают также взаимное расположение свариваемых элементов панели по вертикали.
Транспортировка и зажим под сварку труб осуществляется прижимными боковыми роликами.
На верхней траверсе установки смонтированы кассета с проволокой и бункер с флюсом.
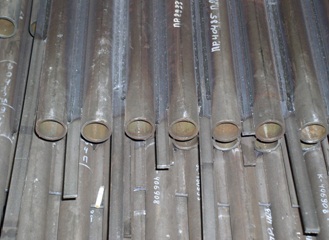
Проходная установка для сварки панелей обеспечивает получение панелей, не требующих правки по плоскости и ребру, так как сварочное устройство работает по принципу роликовой правильной машины; кроме того важна последовательность сварки отдельных труб в панель.
При наличие на сварочной установке двух сварочных головок трубы с проставками чаще всего сначала сваривают попарно (а), затем в небольшие панели из четырех труб и в панели из восьми и далее 16 труб. В этом случае за базу панели принята «двойка».
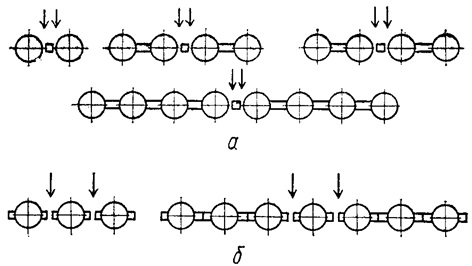
Для плавниковых труб за первый элемент панели может быть принята «тройка». Далее можно образовать панель из двух «троек» и одной трубы между ними, т.е. «семерку» (б).
Таким образом, количество труб в первоначальном элементе панели зависит от числа сварочных головок и уровня технологии сварки, обеспечивающей получение панелей с допустимыми деформациями по ребру и достаточно точным шагом между трубами. Допуск на шаг между трубами составляет 0,5 мм.
Скорость сварки панелей на сварочных установках проходного типа достигает 90 м/ч.
Производственный участок для изготовления газоплотных панелей обычно оборудован несколькими сварочными установками.
Одни из них позволяют сваривать панели шириной 800 мм, причем на одной установке выполняется сварной шов с одной стороны, далее панель кантуется и поступает на очередную установку, где происходит сварка с другой стороны. На следующих сварочных установках можно изготавливать панели шириной 1600 мм.
Дальнейшее укрупнении панели возможно на портальной сварочной установке. На этой установке (в отличие от установок проходного типа) панель в процессе сварки остается неподвижной, а перемещаются сварочные головки вместе с порталом.
Изготовление панелей возможно и на портальной установке. Перед сваркой на стенде портальной установки выкладывают и закрепляют все трубы панели. Сварку труб в панели начинают от середины, для чего целесообразно под одним порталом иметь два сборочных стенда: на одном из них можно производить сборку труб в панель, а одновременно на другом выполнять сварку панели. Далее портал перемещают для производства сварки на первый стенд, а второй освобождают под сборку. Этот способ сварки требует трудозатрат на 10-20% больше.
Следующей операцией является обрезка сваренной панели по ширине. Для этой цели служит портальная газорезательная установка, имеющая два резака. Обрезку панели по ширине производят одновременно с двух сторон.
На этой же установки можно вырезать окна в панели под амбразуру.
Далее панель обрезают по длине в размер, указанный на чертеже. Обрезку выполняют дисковой пилой.
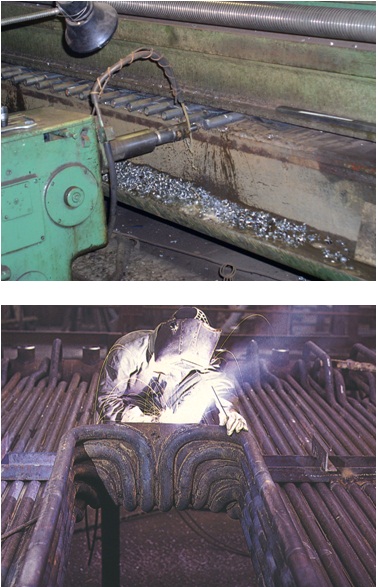
После обрезки панели необходимо обработать концы ее труб под приварку гладких элементов (ножек), соединяющих панель с коллекторами. Лучше всего для этой цели применить угловые машинки (которые имеют ось вращения рабочего органа перпендикулярную к оси машинки).
Для обработки торцов труб панели могут быть использованы специальные сверлильные или расточные станки.
Во многих панелях стен котельного агрегата должны быть предусмотрены разводки труб под лючки, амбразуры, лазы. Эта операция очень трудоемка. Все работы выполняются вручную.
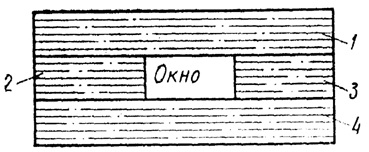
Возможен еще один вариант образования окон в панели, когда их получают набором элементов 1-4. В этом случае изготавливают элементы панели с тем, чтобы, собрав их в определенной последовательности, получить нужный проем под установку труб разводки.
Готовые панели поступают на гибку, которая выполняется на специальном оборудовании.
Гидравлическое испытание
Все элементы поверхностей нагрева подвергают обязательному гидравлическому испытанию.
Иногда однократное испытание не выявляет дефектов сварки или металлургических дефектов, а во время второго или третьего испытания неожиданно появляется течь. Поэтому для наиболее ответственных изделий рекомендуется производить трехкратное гидравлическое испытание.
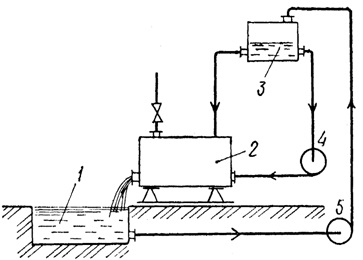
Трубные элементы поверхностей нагрева обычно подвергаются гидроиспытанию дважды: первый раз в виде змеевиков и труб и второй раз после сварки этих элементов в блок. В случае обнаружения течи или потения дефектное место сварочного стыка или трубы ремонту не подлежит, а должно быть обязательно вырезано, и на это место установлена вставка из трубы.
Гидравлическое испытание производится путем наполнения змеевика или трубы водой и подъема в нем давления до 1,25-1,5 от величины давления при котором в дальнейшем должен работать змеевик.
Гидравлическое испытание выполняется на специальном стенде, представляющем собой огороженный металлическими щитами участок цеха с необходимым оборудованием для заливки воды и создания давления. Для исключения больших потерь воды стенд оборудован оборотной системой водоснабжения, состоящей из двух баков 1, 3, насосов 4, 5 и арматуры. Один из баков (верхний) 3 расположен на высоте 6-7м. Из него вода поступает в испытуемое изделие 2. После проведения испытания вода по наклонному бетонному полу стенда пройдя простейший фильтр, стекает во второй бак (нижний) 1, который находится ниже уровня пола стенда. Из этой подземной емкости насосом 5 вода перекачивается в верхний бак. Для подогрева воды в зимнее время в верхнем баке монтируется змеевик, обогреваемый паром или горячей водой.
Проведение гидравлического испытания связано с опасностью для окружающих и лиц, выполняющих это испытание. Поэтому стенд огражден металлическими щитами высотой 2м; кроме того, желательно, чтобы внутри стенда эти щиты были обшиты деревом или резиной для предотвращения рикошета вылетевшей заглушки. Во время испытания на двери стенда вывешивается плакат: «Внимание! Идет испытание. Вход запрещен».
При заливе воды в испытуемое изделие необходимо правильно выбрать место, куда будет заливаться вода, а также положение изделия на стенде с тем, чтобы исключить возможность образования в изделии воздушных «мешков». Для этой цели применяют специальную заглушку с отверстием, закрываемым колпачком, позволяющим выпускать воздух.
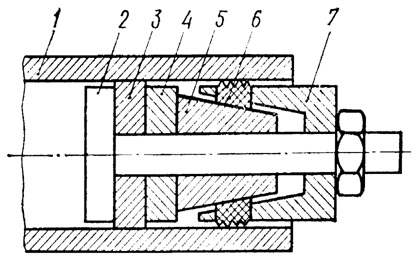
При гидроиспытании концы трубы или змеевика заглушаются специальными «ершовыми» заглушками. При затягивании гайкой конус 5 распирает рифленые «ерши» 6, помещенные в корпус 7, а шток 2 – резиновую манжету 3 внутри трубы 1. Между манжетой 3 и конусом 5 помещена шайба 4. Заглушка удерживается внутри трубы за счет сцепления рифленых «ершей» с внутренней стенкой трубы, а уплотнение создается резиновой манжетой. При использовании «ершовых» заглушек их следует устанавливать тогда, когда убедились, что весь змеевик заполнен водой и воздушные пробки отсутствуют.
Обнаруженные при гидравлическом испытании дефекты исправляются только после того, как давление будет снижено до нуля. Для качественного исправления брака вода из изделия должна быть слита. После исправления любых дефектов изделие подвергается повторному гидравлическому испытанию.
По окончании испытания из изделия сливают воду и тщательно осушают его внутренние полости. Оставшаяся вода вызывает коррозию металла, а большое количество ее в зимний период может привести к размораживанию (разрыву) труб. Удаление воды и просушивание осуществляется продувкой сжатым воздухом под давлением 300-400 кПа.
Операция гидравлического испытания заканчивается прогонкой по каждой трубе или змеевику контрольного шара диаметром 0,8 внутреннего диаметра трубы. Для улавливания шара на конец трубы обязательно надевается шарикоуловитель.
Сборка змеевиков в пакеты
После гидравлического испытания змеевики поступают на сборку в хомуты и стойки, т.к. на участок сборки блоков змеевики поступают в виде пакетов, которые объединяют в себе до четырех и более отдельных змеевиков.
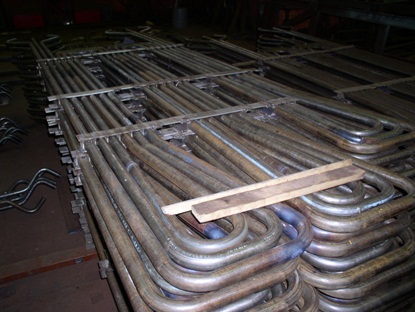
Операция сборки в пакеты выполняется на полу цеха, сварка хомутов и стоек между собой производится вручную электродуговой сваркой. Эта операция требует большой площади для раскладки змеевиков и постоянного наличия грузоподъемного механизма для подачи и уборки с рабочего места змеевиков.
На некоторых котельных заводах операцию сборки змеевиков в пакеты совмещают с операцией плазировки сваренных змеевиков. В этом случае гидравлическое испытание змеевиков происходит в пакетах, что вызывает дополнительные трудности при ремонте дефектных змеевиков, т.к. приходится вытаскивать змеевик из пакета для возможности его ремонта. В связи с этим совмещение операций плазировки и сборки в пакеты не всегда целесообзазно.
Собранные в пакеты змеевики поступают на комплектовочный участок, где укладываются в соответствии с отправочной документацией.
Заключительные операции
Окраска трубных поверхностей нагрева чаще всего производится с помощью пульверизатора. Трубы экрана, водо- пароперепускные трубы раскладываются в ряд на стеллаже высотой 500-700 мм и окрашиваются с одной стороны. После этого переворачивают трубы другой стороной и выполняют окраску этой стороны. Такой метод окраски малопроизводителен и сильно загрязняет окружающее пространство.
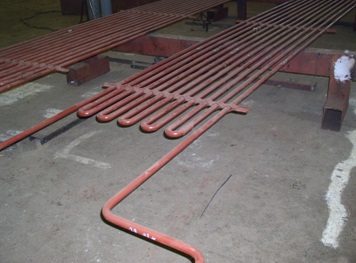
Окраску экранных труб производят после сборки их в блоки, т.к. топочные блоки, как правило, представляют собой панельную конструкцию, и трубы могут быть достаточно эффективно прокрашены в блоке. Кроме этого, при сборке топочных блоков имеет место большое количество сварочных работ на трубах, и если трубы поступили на сборку окрашенными, то необходимо удалить краску для обеспечения качественной сварки.
Наоборот, блоки водяного экономайзера и пароперегревателя из-за плотного расположения змеевиков трудно покрасить в собранном виде. Поэтому змеевики поступают на сборку в блоки уже окрашенными.
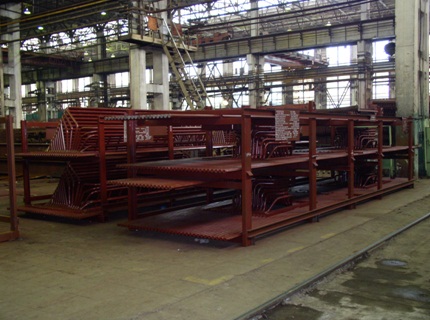
Механически обработанные поверхности труб и змеевиков подвергаются консервации на время транспортировки и хранения на монтаже.
Консервации подлежат фаски на концах змеевиков и труб. После нанесения на них слоя консервации (технический вазелин) концы змеевиков и труб закрываются металлическими или пластмассовыми заглушками, чтобы внутрь змеевика или трубы не попали посторонние предметы.
Маркировка змеевиков и труб производится быстросохнущей несмываемой краской. На змеевике или трубе наносится номер чертежа, номер котла или заказчика.
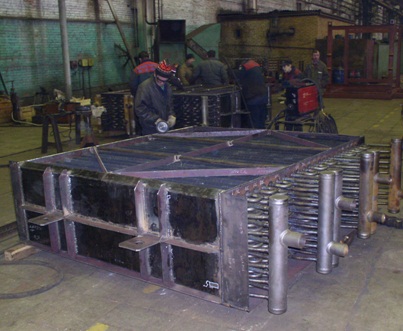
Упаковка змеевиков выполняется через деревянные прокладки, связанные между собой шпильками с гайками.
В случае наличия в пути следования к заказчику многих перегрузок упаковка змеевика производится в металлический контейнер, сваренный из профильного металла. На пакет змеевиков или контейнер привязывается маркировочная бирка с указанием номера чертежа и котла.