Контроль за металлом и сварными соединениями в процессе эксплуатации
В процессе эксплуатации осуществляется контроль за трубопроводами, коллекторами трубами поверхностей нагрева и другими деталями, если они работают при температуре пара 450 °С или более высокой. Контролю подлежат стационарные трубопроводы, элементы котлов и трубопроводы в пределах турбин. В несколько меньшем объеме проводятся наблюдения за трубопроводами питательной воды и водоперепускными трубами в пределах котлов энергоустановок с рабочим давлением 90 атм. и выше. Ответственность за выполнение контроля возложена на главных инженеров электростанций и начальников цехов, в ведении которых находится соответствующее оборудование. Объем контроля определяется «Инструкцией по наблюдению и контролю за металлом трубопроводов и котлов» (СЦНТИ ОРГРЭС). Мероприятия по контролю за металлом, требуемые инструкцией, включаются в график капитальных и текущих ремонтов оборудования. По окончании работ по контролю металла составляется акт, в котором фиксируется фактически выполненный объем работ по контролю металла и его основные результаты.
В процессе эксплуатации подвергаются:
a) осмотру все корпуса арматуры и другие литые детали паропроводов Dу 100 мм во время каждого ремонта после снятия тепловой изоляции, а на 25% из них должна быть проведена в местах резких переходов цветная или магнитная дефектоскопия;
b) визуальному осмотру и контролю средствами дефектоскопии гибы труб главных паропроводов и горячего промперегрева в объеме 50% через каждые 50 тыс. ч.;
c) визуальному осмотру после снятия тепловой изоляции через каждые 50 тыс. ч. коллекторы пароперегревателей, выполненные из легированных сталей, коллекторы пароперегревателей имеющие впрыскивающие пароохладительные устройства, осматриваются во время каждого капитального ремонта;
d) визуальному осмотру трубы поверхностей нагрева и их сварные соединения во время ремонта и при гидравлическом испытании.
Под действием высоких температур и напряжений в процессе эксплуатации происходит увеличение диаметра паропроводов, паросборников, коллекторов и змеевиков пароперегревателей. На электростанции составляется схема паропроводов, в которой указываются места измерения остаточных деформаций. Места измерения деформаций должны располагаться на прямых участках длиной более 1,5 м посередине между сварными соединениями и фланцами. Расстояние от охватывающего пояса подвески или опоры паропровода должно быть не менее 0,7 м, т.к. сварные соединения с усилением сварного шва, охватывающие пояса и фланцы, препятствуют свободному развитию ползучести.
Все места измерения должны иметь надежную съемную тепловую изоляцию с такой же теплопроводностью, какую имеет и тепловая изоляция на остальных участках паропровода. Почему это так важно. Если съемная изоляция значительно менее теплопроводна, то в месте измерения деформации температура трубы окажется выше температуры в других местах. Поэтому в этом месте ползучесть будет протекать быстрее. Если же теплопроводность съемной изоляции значительно больше теплопроводности изоляции всего остального паропровода, то температура металла в месте измерения деформации будет меньше. Ползучесть в этом месте будет развиваться медленнее, чем в остальных частях паропровода.
Под воздействием длительного пребывания при высокой температуре структура и свойства стали могут существенно меняться. Эти изменения вызывают увеличение скорости ползучести и сокращают срок службы. Поэтому необходим периодический контроль структуры и свойств металла паропроводов и сварных соединений.
Техника контроля
Каждый паропровод имеет прямой контрольный участок, из которого вырезают контрольные образцы для исследования структуры и свойств основного металла и сварных соединений. На этом же участке паропровода из перлитной или ферритно-мартенситной стали проводят детальный контроль за ползучестью по бобышкам при помощи микрометров соответствующих типоразмеров.
Контрольные участки располагаются, как правило, на главных паропроводах вблизи котла в легко доступном месте.
На остальных участках паропроводов из перлитных или ферритномартенситных сталей бобышки устанавливаются на скобе под один размер.
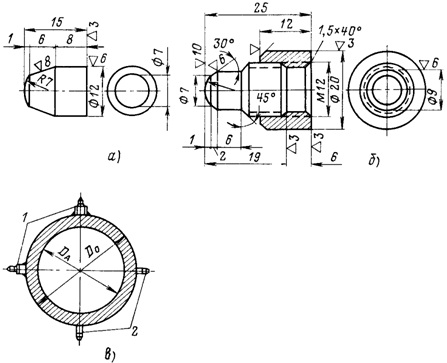
Реперы для измерения ползучести паропроводов: а – репер для непосредственной при-варки к трубе;
б – репер с резьбовой втулкой для установки первоначального размера; в – схема расположения реперов на паропроводе.
Бобышки со втулкой (привариваемые сверху и сбоку трубы) дают возможность подогнать после приварки расстояние между бобышками под один размер с точностью до 0,1-0,2 мм.
Сферическая часть бобышек должна быть отполирована. При измерениях бобышки очищают от грязи и пыли (для очистки нельзя применять наждачную бумагу и напильники). После установки бобышек для определения фактической величины эллиптичности в месте измерения деформации ползучести микрометром измеряют диаметр труб.
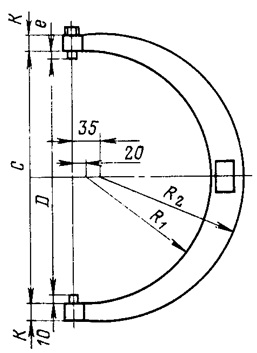
Остаточную деформацию паропроводных труб, выполненных из аустенитных сталей, измеряют непосредственно на самих трубах и поэтому бобышек к ним не приваривают.
В процессе эксплуатации расстояние между бобышками на всех участках паропровода кроме контрольного, измеряют предельными скобами. Используют одни и те же скобы, но губки меняют. По первым сменным губкам устанавливают бобышки. Вторые сменные губки позволяют измерить расстояние между бобышками, которые на 0,5% наружного диаметра больше начального установленного, и таким образом определить момент, когда деформация ползучести паропровода достигнет 0,5% (скоба со старыми сменными губками не проходит над бобышками). Третьи сменные губки позволяют определить момент, когда суммарная остаточная деформация паропровода достигает 1%.
На действующих электростанциях, на которых бобышки не были установлены под один размер до эксплуатации, остаточную деформацию определяют микрометром.
Измерение остаточной деформации всех труб паропровода из аустенитной стали производится при помощи микрометров. Для удобства измерения на поверхности этих труб напильником снимают небольшие площадки глубиной 0,3-0,5 мм. Чтобы исключить влияние теплового расширения трубопровода на измеряемую величину остаточной деформации, все измерения необходимо проводить после того, как паропровод остынет до температуры ниже 50°С.
Результаты первого и последующих измерений записывают в шнуровую книгу паропровода, зарегистрированную в инспекции Госгортехнадзора, и в специальный формуляр. На вновь пускаемых агрегатах второе измерение производят через год, последующие измерения – при капитальных ремонтах, но не реже одного раза в 2 года.
Если остаточная деформация паропровода достигла 1%, необходимо тщательно его исследовать. Для этого вырезают куски трубы длиной не менее 300 мм. На образцах, изготовленных из вырезанного куска трубы, исследуют микроструктуру и механические свойства стали и производят карбидный анализ, который позволяет определить количество карбидообразующих легирующих элементов, оставшихся в твердом растворе и перешедших в карбиды.
Вопрос о возможности эксплуатации паропровода, накопившего остаточную деформацию 1% или более, решается компетентной комиссией, собираемой главным инженером электростанций.
Наряду с паропроводами, паросборниками и коллекторами следят также за ползучестью змеевиков пароперегревателя (ПП), так как температура перегретого пара колеблется в довольно широких пределах. При нарушениях режима работы котла возможны существенные отклонения температуры перегретого пара от расчетной. Для предупреждения аварийных остановов котла из-за разрывов змеевиков пароперегревателей необходимо систематически контролировать накопление в них остаточной деформации.
Остаточная деформация контролируется скобами. Просвет между губками скобы контроля змеевиков из углеродистой стали должен быть больше номинального dн трубы на 3,5%, а для змеевиков из легированной стали на 2,5%. Места измерения — змеевика очищают без применения напильника. Диаметр змеевиков контролируют в зоне максимальных температур обогреваемой стенки пароперегревателя по двум взаимно перпендикулярным диаметрам. Измерение диаметра трубы необходимо производить в одних и тех же местах.
Первое измерение проводят непосредственно после монтажа, последующие – при капитальных ремонтах. Участки с деформацией превышающей допустимую (скоба не проходит) необходимо заменить новыми.
Снижение надежности труб поверхностей нагрева может происходить из-за утонения стенки вследствие коррозии и эрозии. Целесообразно проводить периодические вырезки из поверхностей нагрева в тех местах, где осуществлялись вырезки при входном контроле. Если произошло утонение стенки, при котором уже не удовлетворяется условие прочности при поверочном расчете по «Нормам…» , то поверхность нагрева необходимо заменить.
Размещение контрольных участков главных паропроводов должно предусматриваться при проектировании. Длина труб для контрольного участка должна быть на 300-500 мм больше проектной. Для исследования структуры и свойств металла в исходном состоянии от одного конца трубы отрезают кусок длиной 300-500 мм. Определяют: химический состав по элементам указываемым в сертификате и производят карбидный анализ. Твердость измеряют прибором Бринелля на поперечном сечении. Испытания на растяжение проводят при комнатной и рабочей температурах, ударную вязкость определяют только при комнатной температуре.
Затем исследуют микроструктуру и определяют количество неметаллических включений. Схема вырезки образцов выглядит следующим образом:
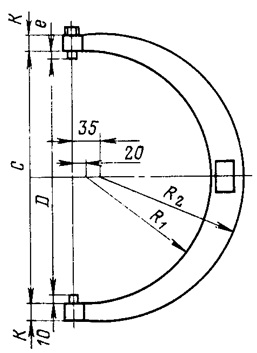
Схема разрезки кольца трубы на образцы: 1- образец для испытания на растяжение; 2 – образец для испытания на ударную вязкость; 3 – образец для карбидного анализа; 4 – образец для микрошлифа
Если труба тонкостенная и поперечные образцы вырезать нельзя, то испытания проводят на продольных образцах. При этом образцы должны быть удалены от среза конца трубы не менее чем на 50 мм. Это необходимо для исключения зоны термического влияния газовой резки.
Микроструктуру исследуют и фотографируют на продольных и поперечных шлифах при увеличении в 100 и 500 раз.
Все результаты заносят в паспорт.
Для контроля структуры и свойств металла образцы из контрольного участка необходимо вырезать через каждые 3 года.
Паропроводы, паросборники, коллекторы из молибденовой стали (15М, 16М, и др.), работающие при температурах превышающих 450 °С проверяют на графитизацию. Графитизация чаще всего поражает зону термического влияния и участки, подвергшиеся холодной деформации.
Для исследования микроструктуры металла разработано приспособление, позволяющее вырезать полушаровой фрезой образцы типа «лодочка». В образец должна попасть зона термического влияния сварки. Места вырезки образцов завариваются электросваркой. Стружку, полученную из «лодочки», растворяют в кислоте. Если имеется свободный графит, то он выпадает в осадок. Обследование паропроводов на графитизацию проводят один раз в 3 года. При обнаружении графита хотя бы в одном стыке все стыки должны быть проверены ультразвуком.
Сварные стыки паропроводов из аустенитной стали осматривают при каждом капитальном ремонте. Сварные стыки паропроводов из перлитной стали должны контролироваться УЗД один раз в 5 лет.
В последние годы для наблюдения за металлом в эксплуатации все шире внедряются приборы, не требующие вырезки образцов.
Для контроля микроструктуры используются переносные микроскопы, укрепляемые на паропроводе.