Термическая обработка сталей — 1 часть
Основные виды термической обработки сталей
Основными видами термической обработки являются отжиг, нормализация, закалка и отпуск.
1. Закалка
Назначение закалки- получение высокой прочности и твердости.
За счет чего это происходит? В доэвтектоидной стали за счет мартенситной структуры (Feα(C)). В заэвтектоидной стали – структуры мартенсита (Feα(C)) и цементита вторичного Fe3C.
После закалки пластические свойства (δ, ψ) и ударная вязкость (ан) низкие.
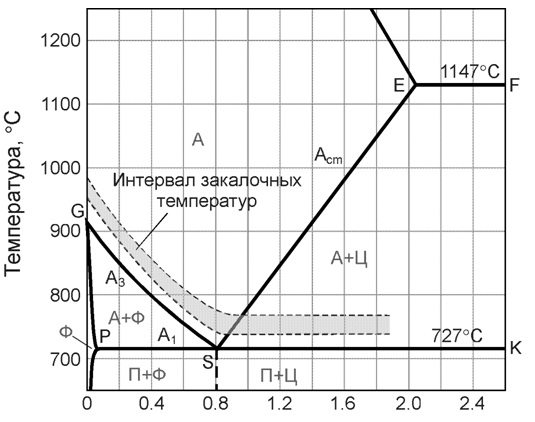
При закалке доэвтектоидной стали (см. рис.) нагрев ведут до температуры 30÷50°С выше Ас3 с последующим резким охлаждением. В результате закалки доэвтектоидной стали получается мартенситная структура. Она обеспечивает наибольшую прочность и твердость.
При закалке заэвтектоидной стали нагрев ведут до температуры 30÷50°С выше Ас1 и также резко охлаждают. Структура этой стали (мартенсит + цементит вторичный) обеспечивает наиболее высокую твердость.
Цементит тверже мартенсита НВЦ=800, НВм=650 в углеродистой стали с 0.5%С.
Рассмотрим, почему указанный интервал температур является оптимальным.
Нагрев доэвтектоидной стали под закалку ниже Ас3, но выше Ас1 приводит к частичной закалке. Зерна, которые в процессе нагрева и выдержки превратились в аустенит, после резкого охлаждения превратятся в мартенсит. Но при этом сохранятся не претерпевшие превращения при нагреве зерна феррита. Т.е. получится структура:
МАРТЕНСИТ (650НВ) + ФЕРРИТ (80НВ)
твердая структура + мягкая структура
Это — брак закалки.
Нагрев до температуры значительно превышающей Ас3, может вызвать перегрев или даже пережог. При этих температурах происходит рост аустенитного зерна и, следовательно, затем после охлаждения получается грубая крупноигольчатая структура мартенсита, обладающая очень низкой вязкостью.
Нагрев заэвтектоидной стали под закалку ниже Ас1 не вызывает образования аустенита, а резкое охлаждение при таком нагреве не приводит к закалке. Сталь получится мягкой. Нагрев существенно выше Асm вызовет растворение вторичного цементита и как следствие рост зерна аустенита и снижение твердости после закалки. Одновременно при слишком высоком нагреве будет больше остаточного аустенита, что также приведет к снижению твердости.
Именно этими обстоятельствами и определяется интервал закалочных температур.
Чтобы произошло превращение аустенита в мартенсит, сталь необходимо после нагрева и выдержки при температуре закалки охладить со скоростью выше критической Vохл > Vкр.
В качестве закалочных сред применяются:
• вода;
• минеральное масло;
• растворы солей и щелочей в воде.
2. Отжиг и нормализация
Назначение отжига: перекристаллизация и устранение внутренних напряжений. После отжига сталь обладает низкой твердостью, умеренной прочностью и высокими пластическими свойствами.
Различают:
• полный отжиг;
• изотермический отжиг;
• неполный отжиг;
• диффузионный отжиг (гомогенезация);
• низкотемпературный отжиг (высокий отпуск).
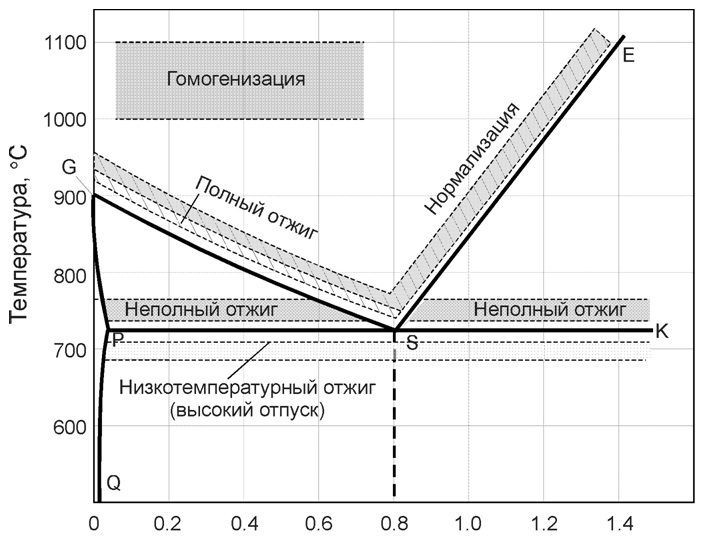
Полный отжиг состоит в нагреве выше линии GSE на 30÷50°С. В результате нагрева и выдержки при этой температуре получается структура из мелких зерен аустенита (т.е. произошла перекристаллизация).
Если сталь нагреть до температуры ниже линии GSE, то в доэвтектоидной стали, кроме мелких зерен аустенита, будут находиться крупные зерна феррита, а в заэвтектоидной стали сохранится сетка цементита.
При нагреве до температур соответствующих линии GSE, превращение будет завершаться медленно, в результате возрастут окисление и обезуглероживание.
Нагрев до температур более высоких, чем 30÷50°С выше GSE, нецелесообразен так как приводит:
1. к перерасходу топлива или электрической энергии на нагрев;
2. к интенсивному росту зерна.
Такой дефект называется перегревом. Он может быть исправлен повторным отжигом.
Нагрев до температур, близких к линии солидус приводит к оплавлению и окислению границ. Это пережог стали – неисправимый дефект.
При отжиге после нагрева и выдержки сталь охлаждают вместе с печью или постепенно снижают температуру печи. При таком медленном охлаждении из аустенита образуются равномерные структуры. В доэвтектоидной стали это структура — Ф+П, в эвтектоидной – П, в заэвтектоидной – П+Ц.
Полный отжиг обеспечивает устранение остаточных напряжений.
Изотермический отжиг состоит в нагреве стали до тех же температур, что и при полном и охлаждении до температуры на 50÷100°С ниже Ас1.Выдержка при температуре ниже Ас1 обеспечивает изотермическое превращение аустенита. После этого сталь можно охладить быстро изменения структуры уже не будет. Деталь можно извлечь из печи и охлаждать на воздухе. Продолжительность пребывания детали в печи сокращается. Применяется вместо полного отжига.
Нормализация заключается в нагреве до тех же температур, что и при полном отжиге, но с охлаждением в спокойном воздухе.
Цель нормализации: получение мелкозернистой структуры и устранение внутренних напряжений.
По сравнению с полным отжигом уровень пластических свойств ниже, а прочность выше.
Структура и свойства металла после нормализации зависят от размера детали. Крупные детали остывают медленно, в них распад аустенита завершается образованием перлита. Мелкие детали остывают быстро. В них аустенит превращается в сорбит.
Разница в свойствах нормализованной и отожженной стали для малоуглеродистых сталей – невелика, для среднеуглеродистых – значительна.
Нормализация обеспечивает большую производительность.
Неполный отжиг заключается в нагреве сплава на 30÷50°С выше А1 (линия PSK) и медленном охлаждении. Его применяют для снятия остаточных напряжений в доэвтектоидных сталях. При неполном отжиге происходит перекристаллизация только перлита. Ферритная составляющая в доэвтектоидных сталях остается неизменной.
Неполный отжиг применяют для снятия напряжений, когда не требуется исправления структуры. Неполный отжиг экономичнее полного. Неполный отжиг заэвтектоидной стали называют сфероидизирующим отжигом.
Диффузионный отжиг (гомогенезация) состоит в нагреве до температуры на 150÷250°С ниже линии солидус, длительной выдержки при этой температуре и последующем охлаждении. Диффузионному отжигу подвергают слитки и крупные стальные отливки.
Цель диффузионного отжига – устранение дендритной и межзеренной ликвации.
При высокой температуре происходит ускорение диффузионных процессов, обеспечивающих выравнивание химического состава в микрообъемах.
Высокая температура вызывает рост зерна, для измельчения которого следует провести полный отжиг или нормализацию.
Поскольку стальное литье из углеродистых сталей содержит от 0,15 до 0,55% углерода, объясняются характерные размеры области диффузионного отжига.
Низкотемпературный отжиг (высокий отпуск) состоит в нагреве до температуры ниже А1 выдержки и медленном охлаждении.
Низкотемпературный отжиг применяется для снятия внутренних напряжений, возникших, в частности, при сварке, в наклепанном металле. Медленное охлаждение необходимо для избежания образования новых внутренних напряжений.
3. Отпуск
Отпуск – нагрев закаленной стали до температуры ниже Ас1 выдержка при этой температуре и охлаждение.
Отпуск применяется для устранения внутренних напряжений и повышения пластичности.
Отпуск в интервале температур 150÷200°С – низкий отпуск. Низкому отпуску подвергаются режущий инструмент и детали, работающие на износ, от которых требуется высокая твердость. В результате низкого отпуска получается отпущенный кубический мартенсит.
Отпуск в интервале температур 350÷500°С называется средним отпуском. Средний отпуск обеспечивает высокие значения пределов упругости, прочности, усталости и высокую ударную вязкость.
Среднему отпуску подвергают, например, пружины подвесок трубопроводов, рессоры. В результате среднего отпуска получается структура — тростит отпуска.
Отпуск в интервале температур 500÷650°С называется высокий отпуск. Предназначен для получения высоких пластических свойств и ударной вязкости при остаточной прочности и твердости. Высокому отпуску подвергают многие детали машин и элементы теплосилового оборудования. В частности, закалке в масле с последующим высоким отпуском подвергают толстостенные паропроводные трубы из некоторых легированных сталей. В результате высокого отпуска получается структура — тростит или сорбит отпуска.
Комплекс механических свойств у стали после закалки с высоким отпуском получается выше, чем после нормализации и отжига.
Свойства углеродистой стали после закалки и отпуска определяются температурой и продолжительностью нагрева при отпуске. Они не зависят от скорости охлаждения после отпуска.
Продолжение читайте во второй части.