Термическая обработка сталей – 2 часть
Первая часть термической обработки была разобрана здесь.
Термическая обработка углеродистой стали
Для получения заданных свойств сталей путем изменения их структуры без изменения формы изделия и химического состава широко используется термическая обработка (ТО). Основные факторы воздействия при термической обработке температура и время, поэтому режим любой ТО можно представить графиком в координатах t-τ.
Термическая обработка состоит из нагрева до заданной температуры выдержки при этой температуре и охлаждении. В большинстве случаев решающая роль в получении желаемой структуры принадлежит охлаждению. Иногда ТО может быть сложнее несколько нагревов и охлаждений. НО в любом случае, изменение свойств сплава, которое создается термической обработкой должно быть остаточным, в противном случае в ТО не было бы никакого смысла.
Для правильного проведения ТО сталей, необходимо хорошо представлять, какие превращения происходят в них, как влияют на эти превращения скорость нагрева, максимальная температура и время выдержки при нагреве и скорость охлаждения.
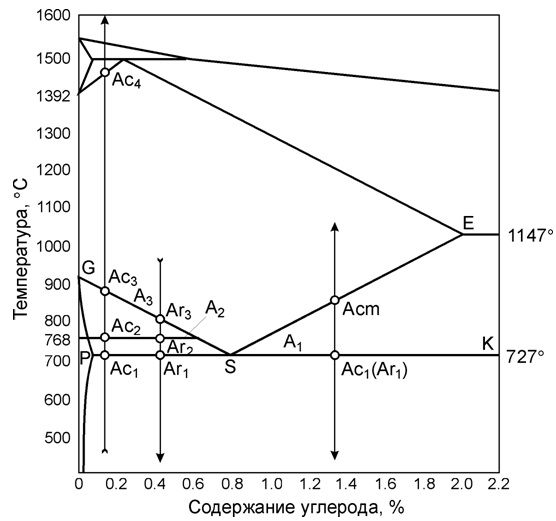
Основой для изучения термической обработки сталей является диаграмма железо- углерод. Так как речь пойдет только о сталях, то рассматриваются сплавы с концентрацией углерода до 2.14%. Верхней границей является линия солидус, поскольку процессы первичной кристаллизации не имеют значения.
Приведем общепринятые обозначения критических точек. Они обозначаются буквой «А». Нижняя критическая точка, обозначаемая А1, лежит на линии PSK и соответствует превращению А-П. Верхняя критическая точка А3 лежит на линии GSE и соответствует началу выпадения или концу растворения феррита в доэвтектоидных сталях или цементита (вторичного) в заэвтектоидных сталях. Чтобы отличить критическую точку при нагреве от критической точки при охлаждении рядом с буквой А ставят индекс:
при нагреве – «с» (Ас);
при охлаждении = «r» (Аr).
Таким образом:
Ас1 – превращение перлита в аустенит [Feα + Fe3C] → Feγ;
Аr1 – превращение аустенита в перлит Feγ → [Feα + Fe3C];
Ас2 – превращение магнитного феррита в немагнитный Feα → Feβ;
Аr2 – превращение немагнитного феррита в магнитный Feβ → Feα;
Ас3 – переход последних кристаллов Feα в Feγ;
Аr3 – появление первых кристаллов Feα из Feγ;
Асm –переход Fe3C (II) ↔ Feγ.
Рассмотрим основные превращения в стали. Фазовые превращения в стали вызваны тем, что вследствие изменившихся условий, например, температуры одно состояние оказывается менее устойчивым, чем другое.
Рассматривая структурные превращения в стали, необходимо указать, что основными являются три структуры, а переход их из одной в другую характеризует основные превращения. Эти структуры:
аустенит – твердый раствор углерода в γ- железе (Feγ);
мартенсит – твердый раствор углерода в α-железе (Feα);
перлит – эвтектоидная смесь феррита и карбида [Feα + Fe3C].
При термообработке стали наблюдается четыре основных превращения:
I. Превращение перлита в аустенит, протекающее выше точки А1:
Feα + Fe3C → Feγ.
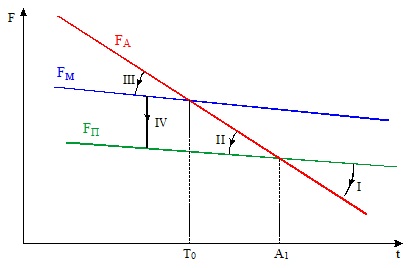
Схема изменения свободной энергии аустенита (FА), мартенсита (FМ) и перлита (FП) с изменением температуры
При температурах выше температуры стабильного равновесия аустенит-перлит из трех основных структур минимальной свободной энергией обладает аустенит.
II. Превращение аустенита в перлит, протекающее ниже точки А1:
Feγ → Feα + Fe3C.
III. Превращение аустенита в мартенсит:
Feγ → Feα.
Протекает ниже температуры Т0. При температуре Т0 более устойчивой фазой является перлит, но работа для образования мартенсита требуется меньшая, поэтому сначала аустенит превращается в мартенсит, а уже потом в перлит. Таким образом аустенитно-мартенситное превращение в данном случае является промежеточным в процессе перехода аустенита в перлит.
IV. Превращение мартенсита в перлит:
Feα → Feα + Fe3C.
Оно происходит при всех температурах так как при любых t Fм > Fп.
Образование аустенита (первое основное превращение)
Превращение перлита в аустенит в полном соответствии с диаграммой состояния Fe-Fe3C может совершаться лишь при медленном нагреве.
В условиях обычного нагрева при ТО превращение П→А запаздывает, получается перенагрев. Перенагретый выше критической точки П с различной скоростью в зависимости от степени перенагрева превращается в А. Время превращения перлита в аустенит при разных температурах различно. Луч V2 показывает нагрев стали с какой-то определенной скоростью. Он пересекает линии начала и конца превращения в точках а» и в». Следовательно при непрерывном нагреве со скоростью V2 мы зафиксируем превращение, протекающее в интервале температур от точки а» до точки в». Если нагрев был медленным, то луч V1 пересекает кривые превращения при более низких температурах (точки а’ и в’), превращение произойдет тоже при более низких температурах.
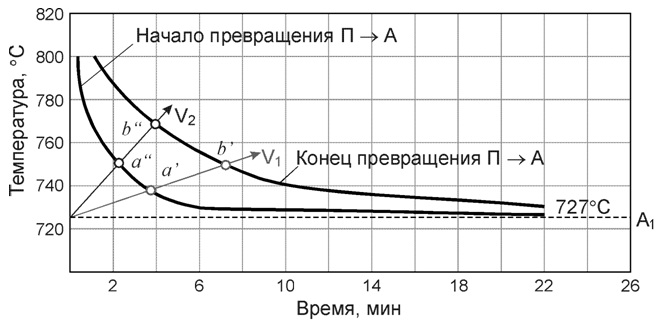
Кривые начала и конца превращения, асимптотически приближаясь к горизонтали А1 пересекут ее в бесконечности. Нагрев с бесконечно малой скоростью пересечет горизонталь А1 в бесконечности, где сливаются кривые начала и конца превращения и где превращение перлита в аустенит произойдет в одной точке при постоянной температуре (t=const). Это, очевидно, и будет случай равновесного превращения по диаграмме Fe-Fe3C. Реальные превращения происходят в интервале температур.
Окончание процесса превращения характеризуется образованием А и исчезновением П (Ф+Ц). Однако этот А даже в объеме одного зерна неоднороден. Там где были пластинки (или зерна) перлитного цементита содержание углерода больше, чем в тех местах, где были пластинки феррита. Для получения однородного по составу (гомогенного) аустенита при нагреве требуется не только перейти через точку окончания перлитно-аустенитного превращения, но перегреть сталь выше этой точки, или дать выдержку для завершения диффузионных процессов внутри зерна А.
Скорость описанных реакций зависит от степени дисперсности цементита и от его формы. Чем мельче частицы Ц и следовательно больше их суммарная поверхность, тем быстрее происходит превращение.
Рост зерна аустенита. Начало перлитно-аустенитного превращения сопровождается образованием первых зерен А. Они образуются на границе между ферритом и цементитом – структурными составляющими перлита. Граница весьма разветвлена в 1см3 перлита площадь границы между Ф и Ц несколько м2. Следовательно, превращение начинается с образования множества мелких зерен. Размер этих зерен характеризует величину начального зерна аустенита. Дальнейший нагрев вызывает рост зерен А. Это самопроизвольный процесс (здесь уменьшается суммарная поверхность зерен, т.е. уменьшается поверхностная энергия), высокая температура лишь обеспечивает достаточную скорость.
Различают два типа сталей:
• наследственно мелкозернистую (НМЗ);
• наследственно крупнозернистую (НКЗ).
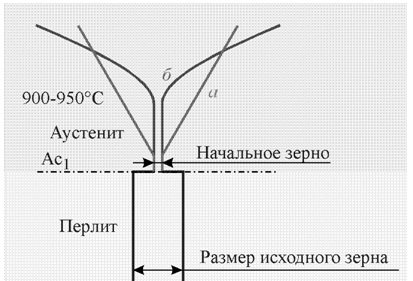
Наследственно мелкозернистая характеризуется малой склонностью к росту зерна, вторая – повышенной склонностью. Переход через А1 сопровождается резким уменьшением зерна. Далее при нагреве зерно аустенита в мелкозернистой стали не растет до 950 ÷1000°С, после чего устраняются факторы, препятствующие росту, и зерно начинает быстро расти. У крупнозернистой стали ничто не препятствует росту зерна, который и начинается вскоре после перехода через критическую точку А1.
Под наследственной зернистостью надо подразумевать склонность зерна к росту.
При температурах немного больше Ас1 зерно А у НКЗ стали больше, чем у НМЗ, а при температурах значительно более высоких у НМЗ стали зерно может оказаться крупнее. Поэтому по размеру зерна в конкретном образце металла нельзя определить наследственную зернистость.
Размер зерна, полученный в результате ТО – ЭТО действительное зерно.
Таким образом, различают:
• начальное зерно – размер зерна А в момент окончания перлитно-аустенитного превращения;
• наследственное (природное) зерно – склонность аустенитных зерен к росту;
• действительное зерно – размер зерна аустенита в данных конкретных условиях.
Влияние размера зерен А на свойства стали в перлитном или другом структурном состоянии заключается в следующем.
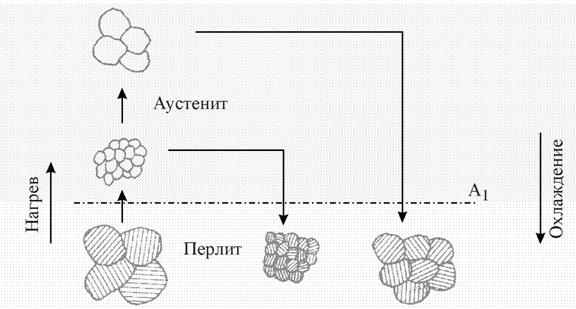
Размер зерен П зависит в первую очередь от размера зерен А, из которых они образовались. Зерна А растут только при нагреве (при последующем охлаждении они не измельчаются). Поэтому максимальная температура нагрева и ее наследственность определяют окончательный размер зерна. Теоретически для определения зернистости необходимо знать зависимость размера зерна от температуры. Практически удобнее наследственную зернистость определять лишь размером зерна. Причем предварительно сталь должна быть нагрета до температуры 930 °С. Затем полученный размер зерна сравнивают со стандартной шкалой. Стали у которых при температуре 930°С размер зерна соответствует № 1-4 стандартной шкалы принято считать НКЗ, а стали с номерами №5-8 –НМЗ.
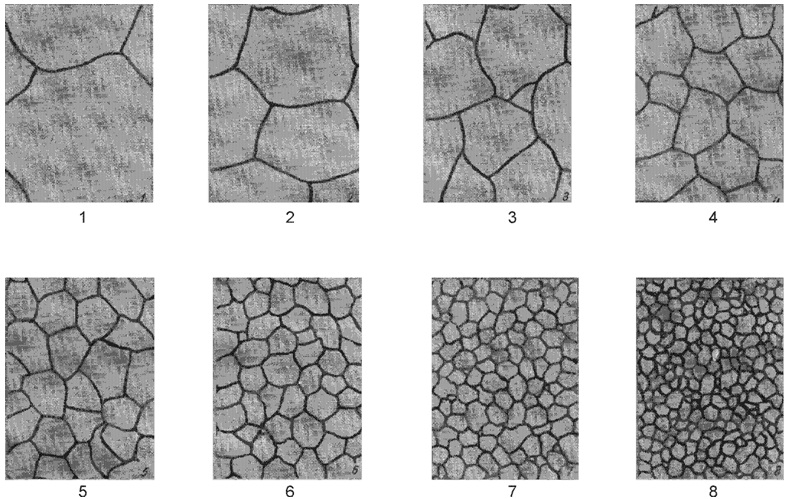
Факторы, влияющие на склонность к росту зерна
Состав стали. Заэвтектоидные стали менее чувствительны к росту зерна, чем эвтектоидные.
Легирующие элементы. Ванадий, титан, вольфрам, молибден и др. уменьшают склонность зерна А к росту.
Способ раскисления. Сталь раскисленная ферромарганцем и ферросилицием –НКЗ сталь, а дополнительно раскисленная алюминием – НМЗ.
Можно утверждать: на свойства стали влияет только действительный размер зерна, наследственный влияния не оказывает. Если у НКЗ и НМЗ сталей в результате термообработки получен одинаковый действительный размер зерна, то и свойства их будут одинаковыми.
Если на свойства стали влияет действительный размер зерна, то технологический процесс горячей обработки определяется наследственным зерном.
НМЗ сталь можно ковать, при более высоких температурах и заканчивать ковку при более высоких температурах, не опасаясь получения крупного зерна. Как правило, все спокойные марки стали — наследственно мелкозернистые, а кипящие – наследственно крупнозернистые.
Распад аустенита (второе основное превращение)
Аустенит устойчив в углеродистых сталях при температуре 727°С. Он может сохраняться в течение некоторого времени и при более низких температурах, но в этих условиях он неустойчив и стремится превратиться в другие структуры.
Превращение аустенита в перлит заключается в распаде аустенита, твердого раствора углерода в γ-железе, на α-железо и цементит:
Feγ = Feα +Fe3C.
При температуре равной А1 превращение аустенита в перлит невозможно FА = FП. Превращение может начаться при некотором переохлаждении, когда FА > FП.
Под степенью переохлаждения аустенита понимают разность между равновесной температурой и температурой, при которой в действительности происходит превращение.
Чем ниже температура превращения тем больше переохлаждение, тем больше ΔF и тем быстрее происходит превращение. НО! В случае перлитного превращения образуются фазы резко отличные по составу от исходной. Feα, который почти не содержит углерода, и Fe3C с 6,67% С.
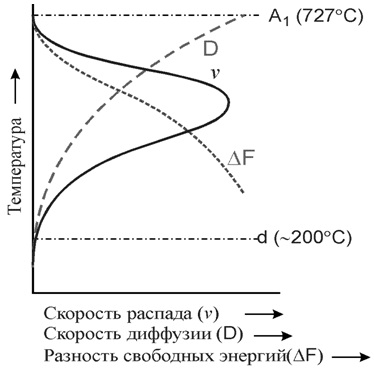
Поэтому, превращение А→П сопровождается диффузией, перераспределением С. Скорость диффузии уменьшается со снижением температуры. Процесс образования перлита это процесс зарождения центров перлита и рост зерен перлита. Следовательно, скорость превращения зависит от скорости роста и числа центров кристаллизации. В точке А1 и ниже 200°С оба параметра равны нулю и имеют максимальное значение при переохлаждении равном 150÷200°С, т.е. если выполнены все условия (аустенит переохлажден ниже А1, FА > FП и D≠0), то процесс начнется и будет происходить в течении некоторого времени.
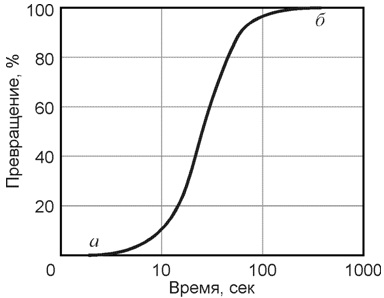
Точка а на кривой показывает момент начала превращения, что соответствует образованию 0,5-1% перлита. Максимальная скорость при 50% образовавшегося перлита. Кинетическая кривая показывает количество образовавшегося перлита в зависимости от времени с начала превращения.
Для анализа превращений, происходящих в сталях при охлаждении, пользуются диаграммой изотермического распада аустенита, которая является основой при выборе способа охлаждения с целью получения заданных свойств. На этой диаграмме по вертикальной оси откладывают температуры, а по горизонтальной – время. Пунктирная прямая, проведенная при температуре 727°С, служит границей устойчивого аустенита.
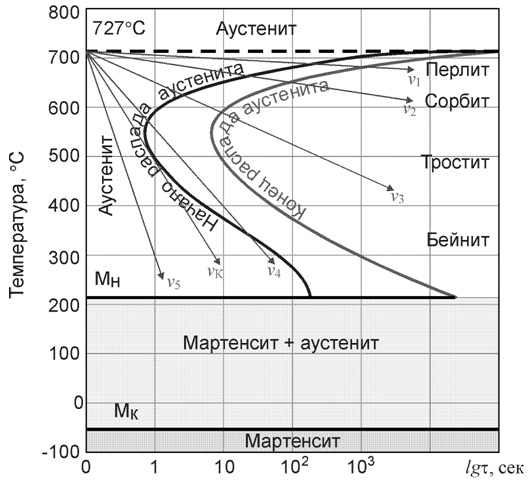
Свойства и строение продуктов превращения аустенита зависят от температуры, при которой происходил процесс его распада.
При высоких температурах, т.е. при малых степенях переохлаждения, получается достаточно грубая смесь феррита и цементита. Эта смесь называется перлитом.
При более низких температурах, и, следовательно при больших степенях переохлаждения дисперсность структур возрастает и твердость продуктов повышается. Мелкопластинчатый перлит, образующийся при температурах 650÷600°С, называется сорбитом.
В районе выступа кривых начала и конца распада получается очень тонкодисперсный перлит, который называется трооститом (троститом).
Таким образом, перлит, сорбит и тростит – структуры с одинаковой природой (феррит + цементит), которые отличаются степенью дисперсности феррита и цементита.
Перлитные структуры могут быть двух типов: зернистые (цементит находится в форме зернышек) или пластинчатые (в форме пластинок). Однородный (гомогенный) аустенит всегда превращается в пластинчатый перлит. Следовательно, нагрев до высокой температуры, который создает условия для образования более однородной структуры, способствует появлению пластинчатых структур. Неоднородный аустенит при всех степенях переохлаждения дает зернистый перлит, следовательно, нагрев до невысокой температуры (для заэвтектоидной стали ниже Ас3) ведет к образованию при охлаждении зернистого перлита.
Таким образом, размер цементитных частиц зависит от температуры превращения аустенита, а форма цементита — от температуры нагрева.
Ниже выступа кривых начала и конца распада аустенита превращение происходит в особую структуру, называемую бейнитом. Он также состоит из мелкодисперсных частиц феррита и цементита. Превращение аустенита в бейнит происходит при относительно низких температурах. Превращение сопровождается увеличением объема, приводящим к большим внутренним напряжениям.
В связи с различным строением продукты распада аустенита обладают разными механическими свойствами. Перлит наиболее пластичен, но твердость и прочность его ниже, чем у остальных структур. По мере повышения дисперсности строения прочность возрастает, а пластические свойства снижаются.
Если охлаждать аустенит со скоростью больше, чем νк (νк – кривая охлаждения, касательная выступу С – кривой), то это приведет к образованию мартенсита.
Мартенситное превращение (третье основное превращение)
Если аустенит переохладить до таких температур, когда γ-решетка, несмотря на наличие растворенного в ней углерода, неустойчива, но скорость диффузии углерода вследствие низких температур так мала, что с ней можно не считаться, то происходит перестройка решетки без выделения углерода
Feγ → Feα
При аустенитно-мартенситном превращении происходит только перестройка решетки без изменения концентрации реагирующих фаз. Превращение является бездиффузионным. Мартенсит есть твердый раствор углерода в α – железе с такой же концентрацией, как и у исходного аустенита.
Так как растворимость углерода в α – фазе всего ≈ 0,01%, то мартенсит является пересыщенным твердым раствором.
Так как превращение бездиффузионное, то углерод из раствора не выделяется и во время превращения происходит только перестройка атомов железа. Расположенные в аустените в виде гранецентрированного куба, они перестраиваются во время превращения в объемноцентрированную решетку.
Для кристаллической структуры мартенсита характерна тетрагональность, т.е. соотношение осей c/a в решетке мартенсита больше 1. Тетрагональность мартенсита – прямое следствие содержания в растворе углерода.
Для мартенсита характерна особая микроструктура. Кристаллы мартенсита представляют собой пластины (в плоскости шлифа они имеют вид игл).
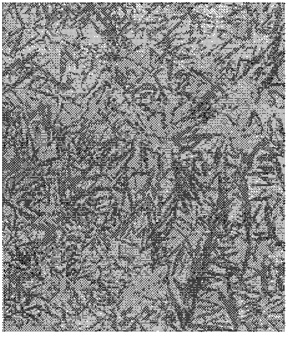
Две характерные особенности отличают мартенситное превращение от других фазовых превращений:
1. бездиффузионность (состав фаз исходной (аустенита) и конечной (мартенсита), одинаков; происходит лишь перестройка решетки;
2. ориентированность (новая фаза – мартенсит закономерно ориентирована относительно старой – аустенита).
Кристаллы мартенсита в стали не зависимо от температуры образуются за очень короткое время (~ 10 -7 с).
Состав стали особенно сильно отражается на температурных точках мартенситного превращения (М и Мк). Увеличение содержания углерода приводит к снижению всего интервала мартенситного превращения. Некоторые легирующие элементы снижают точку мартенситного превращения. Скорость охлаждения не влияет на температуру превращения аустенита в мартенсит, но влияет на протекание мартенситного превращения.
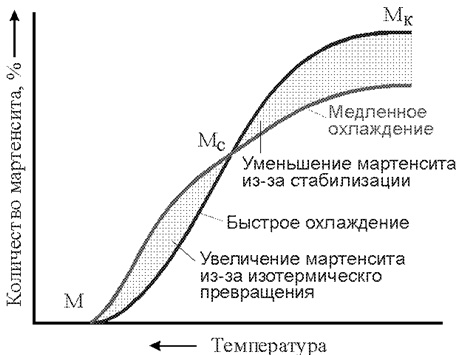
Немного ниже точки М более медленное охлаждение вызывает большую степень превращения. Ниже точки М (приблизительно на 100 °С), когда образовалось довольно значительное количество мартенсита, ускорение охлаждения, наоборот, способствует более полному превращению.
Аустенит, который существует при нормальной температуре наряду с мартенситом называется остаточным аустенитом.
Количество остаточного аустенита в стали, фиксируемое закалкой, зависит от положения мартенситной точки. Чем ниже мартенситная точка, тем больше остаточного аустенита. Поэтому углерод, снижая мартенситную точку, увеличивает количество остаточного аустенита.
Мартенситное превращение в сталях необратимо.
Превращения при отпуске (четвертое основное превращение)
Исходная структура: закаленная сталь, состоящая из тетрагонального мартенсита и аустенита.
Мартенсит является структурой обладающей наибольшим объемом, а аустенит – структурой с минимальным объемом. Следовательно, превращения должны совершаться с объемными изменениями. При превращении мартенсита объем будет уменьшаться (сжатие образца), а при превращении аустенита – увеличиваться (расширение образца).
Дилатометрическая кривая фиксирует превращения при отпуске. Дилатометр – прибор, при помощи которого изучаются изменения длины образца при нагревании и охлаждении).
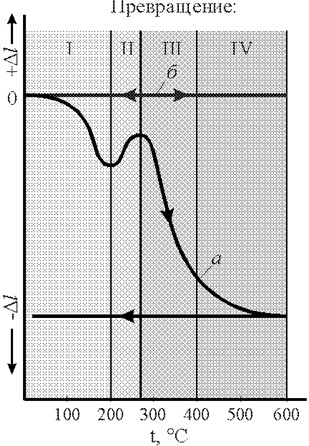
Рис. Дилатометрическая кривая отпуска углеродистой стали (1.2% С), а — закаленная сталь, б — отожженная сталь.
I — выделение углерода из раствора
II — распад остаточного аустинита
III — снятие внутренних напряжений
IV — процесс коагуляции карбидных частиц
Если нагревать в дилатометре отожженный образец, то при отсутствии превращений прибор будет чертить горизонтальную линию б. Отклонения линии а у закаленной стали от горизонтальной линии б свидетельствует о наличии каких-то превращений. Рассмотрим рисунок подробнее. До температуры ≈ 80°С никаких превращений не происходит. С 80°С до 200°С наблюдается сокращение длины. Это так называемое первое превращение при отпуске. Рентгеновский анализ установил, что в этом температурном интервале постепенно уменьшается параметр с решетки мартенсита. Соотношение с/а стремится к единице.
При таком низком отпуске мартенсит, у которого отношение с/а хотя и не равно, но близко к единице, называется отпущенным мартенситом. Следовательно, первое превращение есть превращение тетрагонального мартенсита в отпущенный, почти кубический.
Дальнейший нагрев выше 200°С ведет к иному превращению вызывающему расширение стали. Это так называемое второе превращение при отпуске, захватывает интервал температур 200-300°С. В этом интервале остаточный аустенит превращается в гетерогенную смесь, состоящую из пересыщенного α-раствора и карбида, т.е. остаточный аустенит превращается в отпущенный мартенсит. Это превращение диффузионное (остаточный аустенит распадается на две фазы разной концентрации).
К концу второго превращения, т.е. при 300°С, α-твердый раствор содержит еще около 0,15-0,20% С; наступающее при дальнейшем повышении температуры сжатие указывает на полное выделение углерода из раствора и снятие внутренних напряжений, возникших в результате предыдущих превращений, сопровождающихся объемными изменениями.
Одновременно с этим карбид обособляется и превращается в цементит (Fe3C). Сумма этих изменений характеризует так называемое третье превращение при отпуске.
В третьем превращении при отпуске происходит ряд изменений, приводящих к снятию внутренних напряжений и карбидным превращениям. При 400°С третье превращение заканчивается, и сталь состоит из феррита и цементита. Дальнейшее повышение температуры ведет к коагуляции частиц феррита и цементита.
При отпуске выше 400 °С образуется смесь феррита и цементита, поэтому образующиеся структуры имеют те же названия, что и структуры, полученные в результате прямого распада аустенита на феррит и цементит.
Сталь, отпущенная при 350-500 °С, имеет структуру тростита, при 500-600 °С – сорбит.
Наблюдается существенное различие в смеси феррита и цементита, полученных в результате распада аустенита или мартенсита. В ферритно-цементитной смеси (тростит закалки или сорбит закалки), получающейся при распаде аустенита, цементит имеет пластинчатую форму, а получающийся при распаде мартенсита при температуре 400 °С этой же смеси цементит имеет зернистую форму. Различная форма цементита в ферритно-цементитной смеси предопределяет и различие в свойствах.