Изготовление коллекторов
Технологический маршрут изготовления коллектора:
1. Входной контроль труб корпуса и штуцеров коллектора, а также листа и поковок для днищ.
2. Разметка и резка трубы для корпуса коллектора.
3. Механическая обработка торцов трубы.
4. Сборка днищ с трубой.
5. Приварка днищ.
6. Разметка и сверление отверстий.
7. Установка штуцеров.
8. Приварка штуцеров.
9. Термообработка коллектора.
10. Гидравлическое испытание.
11. Окраска, консервация, маркировка и упаковка коллектора.
Коллектор (камера) парового котла представляет собой цилиндрический сосуд с днищами или без них. Как правило, камера имеет два днища. Если днище отсутствует на одном или обоих концах камеры, значит, на монтаже к этим открытым концам присоединяются трубопроводы пара или воды (торцевой подвод среды).
Цилиндрическая часть коллектора имеет определенное количество штуцеров или отверстий для присоединения с помощью сварки различных труб котлоагрегата. Ранее широко распространенные соединения труб с коллектором с помощью вальцовки в современном энергетическом котлостроении не применяются.
На днищах коллектора обычно также имеются штуцеры достаточно большого диаметра (133 мм), необходимые для осмотра камер в период эксплуатации и для производства некоторых технологических операций на заводе.
Коллектор служит для сбора и раздачи воды или пара различным узлам котла. Различают: коллекторы водяного экономайзера, топочные и пароперегревателя. К особым типам камер относятся камеры пароохладителя, установок собственного конденсата, выносных сепарационных циклонов и им подобные.
Диаметр коллекторов колеблется от 133 до 465 мм, их длина достигает более 10 м, толщина стенки более 40 мм.
Технология производства коллекторов из нелегированной малоуглеродистой стали и легированных сталей перлитного и аустенитного классов в большинстве операций одинакова. Различны операции сварки и термической обработки.
Материалы и требования к ним
Коллектора изготавливаются из труб. Трубы изготавливаются из сталей, выплавляемых в электрических или мартеновских печах. Трубы изготавливают из марок сталей: 20, 15ГС, 15ХМ, 12Х1МФ, 15Х1М1Ф, 12Х2МФСР, Х18Н12Т.
Для изготовления камер используются горячекатаные трубы:
— из углеродистых и легированных сталей диаметром до 465 мм с толщиной стенки до 60 мм;
— из высоколегированных сталей диаметром до 325 мм с толщиной стенки до 32 мм.
В зависимости от заказа коллекторные трубы могут поставляться:
— немерной (любой) длины;
— мерной (определенной) длины.
В случае немерной поставки углеродистые и легированные трубы могут поставляться от 4 до 12 м длины, а высоколегированные трубы от 3 до 9 м.
При определенной номенклатуре изготовляемых коллекторов в целях уменьшения отходов труб целесообразно заказывать трубы мерной длины (в каждой поставляемой партии допускается наличие не более 5% по весу труб немерной длины).
При заказе труб немерной длины производится раскрой поступивших труб в соответствии с чертежами коллекторов. При этом учитывается расположение отверстий и штуцеров на коллекторе, необходимые припуски на обработку концов труб, и, кроме обычной маркировки трубы наносится четкая маркировка частей коллектора по данному чертежу.
Поступившие трубы могут иметь следующие отклонения:
а) по наружному диаметру для горячекатаных труб:
диаметр до 273 мм — ±1%;
диаметр более 273 мм — + 1,25%;
— 1,0%.
б) по толщине стенки для горячекатаных труб:
— из углеродистых и легированной сталей при диаметре более 108 мм —
+20%;
— 5%;
— из высоколегированных сталей:
при диаметре до 140 мм — +15%;
— 10%;
при диаметре более 140 мм — +20%;
— 5%.
Обычно трубы заказывают по наружному диаметру и толщине стенки.
Овальность и разностенность труб не должны выводить размеры труб за пределы допускаемых отклонений по диаметру и толщине стенки.
Допуск по длине мерных труб составляет + 50мм. Существуют ограничения по величине кривизны горячекатаных труб.
На наружной и внутренней поверхностях труб не должно быть трещин, закатов, плен, рванин и глубоких рисок. Эти дефекты должны быть полностью удалены путем местной пологой зачистки шлифмашинкой или сплошной шлифовкой, расточкой и обточкой. При этом толщина стенки в местах удаления дефектов не должна выходить за пределы минимальных допускаемых значений.
Каждая труба подлежит внешнему осмотру снаружи и изнутри. Осмотр наружной поверхности трубы производится без увеличительных приборов. Внутреннюю поверхность трубы осматривают с помощью перископа без увеличения.
Затем каждая труба подвергается контролю физическими методами без разрушения. Этот контроль производится ультразвуковыми и электромагнитными дефектоскопами, с помощью которых выявляются дефекты, расположенные в толще стенки трубы и на ее поверхности.
Каждую трубу из легированных сталей подвергают контролю стилоскопом на содержание легирующих элементов, и после этого на трубу наносится цветная маркировка несмываемой краской. Маркировка представляет собой одну продольную полосу по всей длине трубы.
Концы труб отрезаются под прямым углом. Резка труб диаметром более 114 мм с толщиной стенки более 20 мм из углеродистых и легированных сталей допускается автогенной резкой или пилой горячей резки с последующей зачисткой концов труб от наплывов и грата. При таком способе резки припуск по длине на каждый рез составляет 20мм.
Все трубы поставляются в термически обработанном состоянии.
Каждая труба на заводе-изготовителе труб проверяется на прочность гидравлическим испытанием. Под пробным давлением труба выдерживается в течение времени, необходимого для ее осмотра.
На конце трубы на расстоянии 200-300 мм от концов наносится маркировка:
— товарный знак завода-изготовителя;
— марка стали;
— номер партии труб или номер трубы.
Входной контроль
Поступившие на склад завода трубы прежде всего проверяются на наличие сертификатов о качестве этих труб, полноту отраженных в них сведений о трубах и соответствие этих данных техническим условиям.
Только после этого трубы поступают в производство!!!!
В целях увеличения надежности и повышения качества таких ответственных деталей котлоагрегата, как коллекторы, на котлостроительном заводе трубы подвергают входному контролю. При входном контроле производится внешний осмотр и обмер труб, проверка марки стали легированных труб стилоскопированием, проверка качества металла трубы УЗД.
Для возможности более качественного осмотра, а также удаления слоя консервации трубы подвергают пескоструйной очистке снаружи и изнутри. Очистку производят с использованием металлического или кварцевого песка. Эту операцию выполняют в специальных пескоструйных камерах, снабженных хорошей вентиляцией. Очистка снаружи выполняется достаточно просто и быстро. Для очистки внутренней поверхности труб диаметром 83 мм и более применяют установку Ваку-Бласт.
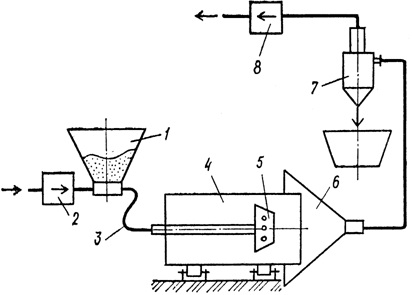
Установка Ваку-Бласт состоит из гибких шлангов 3 с набором сопл 5 для очистки труб 4 различных диаметров. Установка имеет систему регенерации песка, поступающего из бункера 1 под напором вентилятора 2, в которую входят сборный фартук 6 и циклон 7, а также систему очистки воздуха с вентилятором 8 и может быть размещена в любом месте цеха.
Осмотр внутренней поверхности труб производится с помощью переносных перископов различных марок. Перископ РВП-456 предназначен для осмотра внутренних поверхностей труб диаметром от 37 до 400 мм с целью выявления качества поверхности стенок и наличия поверхностных дефектов материала типа трещин, задиров, пористости и др.
Для контроля УЗД коллекторных труб применяется установка «Дон-2». С помощью этой установки выявляется нарушение сплошности материала в стенки трубы. Ультразвуковой контроль обеспечивается перемещением искателей по винтовой линии. Для этого контролируемая труба вращается на кантователе установки, а искатели имеют поступательное перемещение вдоль образующей трубы. Искательная головка состоит из 4-х искателей, 2 из которых служат для выявления поперечных дефектов, а 2 других – для выявления продольных дефектов.
Прошедшие все виды входного контроля трубы поступают на разметку и резку.
Разметка и резка
Разметку труб производят с помощью рулетки, линейки, чертилки, керна и молотка и не представляет сложности.
При разметке следует обратить внимание на то, чтобы на каждой заготовке были клейма марки стали, номера трубы, а также предусмотрен необходимый припуск на механическую обработку торцов.
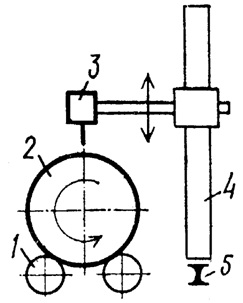
Резка заготовки выполняется обычно ацетилено-кислородной резкой вручную или на полуавтоматических установках. Такие установки могут быть применимы для труб любой толщины как из углеродистой, так и из низколегированных сталей. Установка представляет собой роликовую постель 1, на которую укладывают трубу-заготовку 2, и газорезательную головку 3, с помощью которой производят резку. Роликовая постель снабжена приводом, благодаря которому осуществляется вращение трубы-заготовки. Для лучшего сцепления роликов постели с трубой и невозможности проскальзывания трубы при вращении ролики на поверхности имеют рифление. Газорезательная головка установлена на стойке 4, которая может передвигаться по рельсовому пути 5 вдоль роликовой постели в зависимости от длины обрезаемой трубы. Для возможности настройки головки на резку труб различных диаметров ее можно перемещать по вертикали вверх и вниз с помощью винта. Кислородные и ацетиленовые шланги подвешиваются на специальном кронштейне, чтобы они не мешали при работе и передвижении стойки с газорезательной головкой.
Полуавтоматическая резка, кроме обеспечения качества реза и высокой производительности, позволяет иметь меньшие припуски под механическую обработку торцов камеры по сравнению с ручной резкой.
Зачистив грат после газовой резки и убедившись в полноте клеймения заготовки, детали отправляют на механическую обработку концов трубы.
Механическая обработка кромок
Перед установкой заготовки на станок необходимо произвести разметку трубы под механическую обработку в соответствии с чертежом.
Обработка концов трубы выполняется на токарных станках, причем один конец трубы обычно зажимается в патроне, а другой — в люнете или заднем центре. Правильность выполнения разделки конца трубы проверяется шаблоном.
В последнее время для обработки торцов заготовки коллектора под сварку стали применяться специальные полуавтоматические станки для одновременной обработки обоих концов трубы. Такой станок снабжен двумя резцовыми головками спереди и сзади станка, а труба закрепляется в специальных зажимах, находящихся между этими головками. Однако для эффективной работы такого станка необходимо иметь трубу- заготовку с минимальными допусками на диаметр, толщину стенки, овальность и прогиб.
Днища коллекторов
Днища коллекторов могут быть плоскими, эллиптическими, сферическими и изготавливаются из поковок или из листа с последующей механической обработкой на токарном или небольшом карусельном станках.
Изготовление штуцеров
Заготовка штуцера отрезается из трубы на токарном станке, затем производится необходимая по чертежу обработка кромок под сварку. Часть штуцеров изготавливается из поковок обычными технологическими приемами механической обработки с использованием широко распространенного универсального оборудования.
Многие коллектора, кроме оговоренных деталей, имеют подвески и уши различной конфигурации. Это плоские детали, изготовленные из листовой углеродистой или легированной стали. Обычно они вырезаются кислородно-ацетиленовой резкой с последующей обработкой кромок согласно чертежу. В случае вырезки таких деталей на газорезательном автомате по копирам, как правило, механическая обработка не требуется.
Как было сказано ранее, большинство коллекторов имеет на одном или обоих днищах торцевые штуцеры диаметром 133 мм, которые служат на заводе для удобства проведения некоторых технологических операций, а на монтаже – для ревизии коллекторов. Эти штуцеры заранее привариваются к днищу до общей сборки коллектора. Приварка производится на полуавтоматической установке многослойной сваркой под слоем флюса.
Сборка и сварка коллекторов
На сборку попадают детали, принятые ОТК. Сборку камеры начинают со сборки трубы с днищами. Эту операцию производят на небольших роликовых кантователях, состоящих в зависимости от длины камеры из двух или четырех пар роликов, не имеющих специального привода. При необходимости поворот трубы осуществляется вручную. У некоторых камер разделка кромки днища под сварку имеет по окружности выступ толщиной около 4 мм, который заходит в расточенный конец камеры и центрирует днище с камерой. Необходимый зазор между донышком и камерой устанавливают и контролируют при помощи шаблона. После этого днище прихватывают электросваркой к камере и передают на сварочный участок.
В некоторых случаях для несущественного облегчения операции разметки производят разметку коллектора под сверление отверстий до установки и приварки днищ. Более правильной будет разметка после приварки днищ. Начало отсчета ведется от центров кольцевых швов, поскольку, при сварке кольцевых швов на камере (приварка днищ, стык одной части коллектора с другой при большой общей длине коллектора) наблюдается небольшая усадка, примерно по 2мм на каждый кольцевой стык.
При сборке трубы с днищами необходимо замерить в четырех местах фактическую толщину стенки трубы и заклеймить эти данные на трубе. В дальнейшем эти цифры понадобятся при настройке эталонов для проведения ультразвуковой дефектоскопии кольцевых сварных швов коллектора. При стыковке частей коллектора между собой сварку этих швов производят на подкладных кольцах, которые не удаляются после сварки. Кольцо вытачивается на токарном станке и плотно собирается с концом трубы, при этом зазоры между кольцом и трубой более 1мм не допускаются.
Масштабы современного производства коллекторов, специализация цехов по их изготовлению, унификация конструкций кольцевых стыков создают условия для широкого применения автоматической сварки под флюсом. При высоком качестве сварного соединения и значительном облегчении труда сварщика производительность ее в несколько раз выше ручной сварки, а трудозатраты на 80 -120% ниже.
Все стыки коллектора завариваются сплошным усиленным швом. Шов накладывают в несколько слоев, число которых зависит от толщины стенки коллектора и выбранного режима сварки. Каждый слой шва зачищается от шлака легким молотком или зубилом непосредственно в процессе сварки самим сварщиком.
По приводу для вращения коллектора в процессе сварки сварочные установки делятся на два типа:
1. Установки с приводными роликами, передающими вращение коллектору посредством силы трения.
2. Установки с холостыми роликами и отдельным приводом с кулачковой планшайбой для вращения коллектора.
Оба типа установок имеют свои преимущества и недостатки; поэтому и те, и другие используются в производстве. Однако наибольшее применение находят установки первого типа.
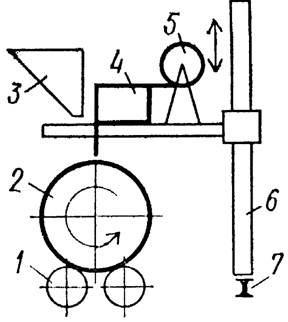
Такая установка состоит из самоходой тележки 6 велосипедного типа, монорельса, гирлянды проводов, рельсового пути 7, расположенного вдоль свариваемого коллектора 2, и кантователя 1 с приводными роликоопорами. Рама самоходной тележки имеет направляющие, по которым вдоль вертикальной оси рамы перемещается каретка. На каретке подвешена с помощью кронштейна сварочная головка 4, а также укреплены бункер для флюса 3 и кассета 5 с проволокой. Сварочная головка укреплена на кронштейне через систему суппортов, которые дают возможность точно корректировать положение электрода во всех направлениях. Самоходная тележка снабжена приводом для передвижения ее по рельсовому пути вдоль свариваемого коллектора. Кантователь состоит из одной приводной и одной холостой пар роликоопор. Холостая роликоопора может передвигаться по специальным направляющим на определенное расстояние от приводной роликоопоры с таким расчетом, чтобы свариваемый стык коллектора находился вблизи роликоопоры. При таком положении кривизна коллектора в меньшей степени сказывается на биении. Приводная роликоопора имеет плавную бесступенчатую регулировку сварочной скорости.
Технические данные установки:
Диаметр свариваемых изделий | мм | 150-600 |
Длина свариваемых изделий | мм | 1500-12000 |
Максимальная масса свариваемых изделий | кг | 5000 |
Скорость сварки | м/ч | 15-45 |
Диаметр сварочной проволоки | мм | 2-3 |
Регулировка скорости сварки | — | плавная |
Сварка производится на постоянном токе обратной полярности. Установку обслуживает один человек. В целях обеспечения надлежащего качества шва после сварки каждого слоя необходима его тщательная зачистка от шлака и осмотр для выявления возможных пороков. После сварки сварщик ставит около шва свое клеймо.
После внешнего осмотра сварных швов производят их проверку ультразвуковой дефектоскопией и исправление обнаруженных дефектов. Контроль сварных швов УЗД производится переносными приборами. Дефектоскопию следует выполнять сразу после приварки днищ к коллектору, до установки и приварки штуцеров, так как во многих конструкциях коллекторов штуцера расположены в непосредственной близости от сварного шва и мешают проведению качественного контроля.
Убедившись в надлежащем качестве сварных швов приварки днищ к трубе, приступают к разметке коллектора под сверление отверстий для установки штуцеров. Разметку выполняют на роликовых кантователях с использованием обычного инструмента для разметки. Если коллектор имеет прогиб, то при разметке следует так располагать будущие отверстия под штуцера, чтобы осевые линии с наибольшим количеством отверстий оказались на выпуклой стороне коллектора. При последующей приварке штуцеров эта выпуклость несколько выправится от напряжений, возникающих в процессе приварки.
Разметка и сверление отверстий
Операция разметки является одной из самых ответственных и трудоемких, поэтому наблюдается тенденция отказа от нее путем использования станков с программным управлением для разметки и сверления отверстий.
На котлостроительных заводах сверление отверстий в коллекторах производится различными способами:
— на обыкновенных радиально-сверлильных станках с применением обычного инструмента; эти станки, как правило, оборудуют быстродействующими пневматическими зажимами, позволяющими надежно закреплять коллектор при сверлении.
— на многошпиндельных станках для сверления отверстий; расположение шпинделей может быть вертикальным, горизонтальным и наклонным.
— с применением различного вида кондукторов для сверления отверстий с одинаковым шагом между ними.
Приварка штуцеров
Следующей операцией при изготовлении коллекторов является установка и приварка штуцеров. Штуцера диаметром до 133мм обычно устанавливают на отверстии в выточку глубиной до 5мм. Штуцера диаметром 133мм и более собирают и приваривают к коллектору с помощью подкладных колец, которые в процессе дальнейшего изготовления коллектора удаляют. Штуцер предварительно собирают с подкладным кольцом, которое приваривают ниточным швом к стене штуцера и затем собирают с коллектором.
Сборку штуцеров производят вручную и контролируют с помощью угольника в направлении оси коллектора, а в перпендикулярном направлении — с помощью уровня. Отклонение штуцера от вертикали допускается в пределах 1 мм. Особо тщательно устанавливают и проверяют два крайних в ряду штуцера. После этого между ними натягивают струну и по ней устанавливают все остальные штуцера этого ряда. При сборке штуцера прихватывают к коллектору электросваркой. Иногда для сборки штуцеров используют сборочные приспособления, позволяющие точнее осуществить сборку.
Приварка штуцеров к коллектору может быть выполнена ручной и автоматической сваркой под флюсом.
При ручной сварке часто первый слой ее выполняют в среде аргона для получения качественного корня шва. При наложении каждого слоя сварки следует тщательно очищать сварной шов от шлака. Штуцера к коллектору приваривают не менее чем в два прохода независимо от катета приварки. Корень шва заваривают электродом диаметром не более 3 мм, последующие слои могут быть наварены электродом 4 мм. Ручная приварка штуцеров к коллекторам — операция массовая и очень трудоемкая. Поэтому вопросу ее механизации уже давно уделяется большое внимание.
Автоматическая приварка штуцеров имеет ряд технологических особенностей, а именно:
1. При приварке электрод должен двигаться по пространственной кривой пересечения цилиндра с цилиндром.
2. Чтобы штуцер не прожигался, требуются очень точное движение электрода по линии сопряжения штуцера с коллектором и стабильный процесс сварки.
3. Для точного движения электрода по линии сопряжения нужна точная база для установки сварочной головки. Наружная поверхность коллектора имеет большие допуски как по эллипсности, так и по кривизне. Кроме того, штуцер, представляющий собой кусок трубы, устанавливают на коллектор вручную, поэтому он тоже не может служить надежной базой.
4. Угол, образуемый стенками штуцера и коллектора, переменный по периметру стыка. Он изменяется от 90 по продольной оси соединения до 110-120 по поперечной оси, что создает неблагоприятные условия для формирования шва.
5. Расплавленный металл и шлак стекают с наклонных стенок круглого коллектора тем интенсивнее, чем меньше диаметр коллектора и больше диаметр штуцера.
Институтом электросварки им Е.О.Патона разработан автомат, предназначенный не только для приварки штуцера, но и для установки его по месту с точным фиксированием положения в перпендикулярном направлении по отношению к коллектору.
При сварке коллекторов из легированных сталей необходим предварительный и сопутствующий подогрев мест сварки равномерно по всему сечению в зоне не менее 100 мм с каждой стороны шва. Так, при сварке коллектора из стали 12Х1МФ обязателен предварительный и сопутствующий подогрев зоны шва до 350-400 С. Подогрев может осуществляться электрическими печами, газовыми горелками или другими средствами, обеспечивающими равномерный нагрев всего сечения. Сопутствующий подогрев контролируется через промежуток времени не более 20 мин.
Если на коллекторе устанавливается большое количество штуцеров, после приварки их коллектор сильно деформируется от сварочных напряжений. Обычно коллектор получает прогиб в плоскости оси, на которой установлено наибольшее количество штуцеров, выпуклой частью от этой оси. Говорят, что коллектор «ведет на сварку», и штуцера оказываются расположенными во впадине прогнувшегося коллектора. В этом случае коллектор необходимо править, что достигается с помощью пресса или (при достаточной квалификации рабочих) путем нагрева ее в определенных местах газовой горелкой. Допускается прогиб коллектора 1,5-4 мм на 1 м длины, но не более 15 мм на всю его длину.
В коллекторах большой длины с большим количеством штуцеров прогиб после их приварки получается настолько большим, что он трудно поддается исправлению, так как этому мешают штуцера. В таких случаях до установки и приварки штуцеров камеру предварительно прогибают в сторону противоположную прогибу от приварки штуцеров. Эту операцию выполняют вручную с помощью газовой горелки или пресса. Степень такого технологического обратного прогиба зависит от длины камеры, толщины ее стенки, количества и расположения штуцеров, схемы их приварки и устанавливается опытным путем.
Одновременно с приваркой штуцеров на коллектор устанавливают и приваривают к нему другие детали типа ушей, подвесок, бобышек и т.п.
Подкладные кольца, с помощью которых собирают и приваривают штуцера, удаляют путем последующей расточки их радиально-сверлильных или расточных станках.
Проведя внешний осмотр всех сварных швов на коллекторе, и исправив дефекты, сварные швы приварки штуцеров к коллектору проверяют неразрушающими методами контроля (ультразвуковой дефектоскопией или просвечиванием) только на штуцерах с внутренним диаметром более 100 мм. Если коллектор имеет детали из легированной стали, необходимо убедиться в соответствии марки используемой стали и наличии легирующих элементов в сварных швах. Проверку производят переносными стилоскопами.
Термообработка коллектора
Термической обработке после сварки для снятия внутренних напряжений подлежат коллектора из углеродистой стали и стали 15ГС при толщине стенки более 35 мм, а также коллектора, изготовленные из легированных и высоколегированных труб. Рекомендуются следующие режимы термообработки после сварки коллекторов:
Марка стали | 20 | 15ГС | 15ХМ | 12Х1МФ | 15Х1МФ | Х18Н10Т |
Температура ТО, С | 600-650 | 650-680 | 680-710 | 730-750 | 730-750 | 1050-1100 |
Для исключения коробления коллектора при нагреве температура печи при посадке в нее изделия должна быть не выше 350 С. Исключение составляют конструкции, которые свариваются с сопутствующим подогревом и должны быть помещены в печь немедленно после сварки. В этом случае температура печи при посадке должна быть не ниже температуры подогрева.
Скорость нагрева при толщине стенки коллектора до 25 мм не должна превышать 200 С/час. При большей толщине скорость нагрева определяется по формуле:
V=5000/S С/час,
где S — толщина стенки, мм.
При нагреве изделий температура различных участков не должна отличаться более чем на 50 С.
Длительность выдержки изделия при температуре должна обеспечивать равномерный прогрев изделия, полноту протекания релаксационных процессов и структурных превращений.
Для коллекторов из углеродистой стали и 15ГС время выдержки при отпуске составляет 2,5 мин на 1 мм толщины стенки, но не менее 30 мин. Для легированных труб время выдержки при отпуске устанавливается из расчета 1,5 мин на 1мм толщины стенки, но не менее одного часа.
Скорость охлаждения изделия должна быть такой, чтобы исключить образование новых остаточных напряжений и коробление конструкции. Максимальная скорость охлаждения для элементов с толщиной до 25 мм не должна превышать 200 С/час. При большей толщине — не более 5000/S С/час.
Для термической обработки сварных соединений допускается применение как общего печного нагрева, так и местного индукционными нагревателями или многопламенными газовыми горелками.
Следует помнить, что даже такая прогрессивная местная термообработка как индукционная влечет за собой образование остаточных напряжений. Необходимо стремиться к тому, чтобы эти напряжения были минимальными.
Во время термообработки должны соблюдаться условия, обеспечивающие свободное расширение изделия и предохраняющие его от пластической деформации под действием собственного веса. При местной ТО сварной стык и прилегающие к нему зоны основного металла должны быть равномерно нагреты по всему сечению с каждой стороны стыка на длине не менее 4S, но не менее 100 мм при толщине стенки коллектора до 30мм и не менее 3 S, но не менее 120 мм при толщине стенки коллектора более 40 мм.
Промежуток времени между сваркой и термообработкой коллектора должен быть минимальным и по возможности не более 72 часов.
Предпочтительнее производить ТО коллекторов в печах с регистрацией температуры нагрева, выдержки и охлаждения.
При местной обработке температура измеряется контактной термопарой или термокарандашом. Зона термообработки должна быть закрыта асбестовой рубашкой.
Механически обработанные кромки деталей коллектора и резьбовые соединения защищаются на время термообработки обмазкой глиной или асбестом.
Гидравлическое испытание коллектора
Для гидравлического испытания коллектор подается на стенд для испытаний.
Гидравлическое испытание коллекторов производится в такой последовательности:
1. Все отверстия в штуцерах заглушаются, за исключением двух: одного — для впуска воды и другого (расположенного в верхней точке коллектора) — для выхода воздуха.
В коллекторах котельного агрегата имеется небольшое количество штуцеров диаметром 133 мм и более. Такие штуцера устанавливают на коллектор с заранее обработанными кромками и после гидравлических испытаний коллектора не обрабатываются. Эти штуцера закрывают с помощью съемных наружных накидных заглушек. У многих коллекторов имеется большое количество (десятки, сотни) штуцеров, которые невозможно закрыть надежными съемными заглушками. Такие штуцера, как правило, диаметром 25-60 мм закрывают приварными заглушками.
2. Коллектор наполняется водой до полного выхода воздуха, т.е. до появления воды из воздуховыходного отверстия, после чего это отверстие заглушается.
3. При помощи гидравлического насоса давление воды в коллекторе поднимают до величины (1,25-1,5) Рраб.
4. Давление воды снижают до рабочего давления, при котором производится осмотр сварных швов коллектора; при осмотре район швов (участок коллектора 100-150 мм с каждой стороны шва) обстукивается молотком весом 1-1,5 кг.
Неплотности сварных швов, а иногда и основного металла коллектора выявляются наличием течи или потения. Обнаруженные дефектные места вырубают при помощи пневматического зубила и заваривают, после чего коллектор вновь подвергают гидравлическому испытанию.
Прошедший испытание коллектор передается на дальнейшую обработку.
Обработка приварных штуцеров и отверстий для труб
Принятый после гидроиспытания коллектор поступает на разметочный стенд. Здесь коллектор устанавливается в горизонтальном положении для разметки штуцеров по высоте под обрезку заглушек. Разметка производится при помощи струны, натянутой между крайними в ряду штуцерами.
Обрезку заглушек производят газовым резаком по линии на 5 мм выше линии разметки. Припуск 5 мм по высоте штуцера оставляется на механическую обработку его торца под монтажную приварку трубы. Эта обработка состоит в подрезке торца и снятии фаски под сварку под углом 25-30. Работа может выполняться на радиально-сверлильных или расточных станках. Размеры штуцеров после обработки проверяют шаблонами.
Часть коллекторов котельного агрегата не имеет штуцеров для присоединения труб (бесштуцерная приварка труб). Отверстия в коллекторе под эти трубы сверлят после его гидравлического испытания.
После обработки концов штуцеров, к которым были приварены заглушки, и сверления отверстий, необходимо очень тщательно очистить внутреннюю полость коллектора от металлической стружки и других посторонних предметов. В противном случае эти загрязнения могут попасть при работе котла в змеевики и трубы, что приведет к недостаточному охлаждению этих мест труб и, как следствие, к их пережогу.
Окраска, консервация, маркировка и упаковка коллектора
Наружная поверхность коллектора окрашивается с целью предотвращения коррозии на период хранения и монтажа.
Перед отправкой заказчику все обработанные механическим способом поверхности деталей коллектора и штуцеров (поверхности трубных и лючковых отверстий, фаски под сварку в штуцерах, зеркала фланцев) должны быть обработаны консервирующей смазкой. После смазки в лючковые отверстия устанавливаются на прокладках и затягиваются гайками лючковые затворы. Отверстия для труб и отверстия в штуцерах закрываются специальными металлическими заглушками.
Готовый коллектор маркируется. Маркировка выбивается непосредственно на коллекторе на расстоянии 100-200 мм от конца. Место для маркировки зачищается шлифовальной машинкой и обводится рамкой светлой несмываемой краской. Место маркировки не окрашивается, а консервируется.