Оптимизация надежности объекта как системы элементов
Недостаточная надежность теплоэнергетического оборудования всегда приводит к нежелательным последствиям, связанным с дополнительными затратами на ремонт и последующие пуски агрегатов, а также к увеличению расходов на создание и эксплуатацию резервных установок. Эти затраты, связанные с устранением последствий отказов, носят системный характер и зависят в первую очередь от:
— конструкции;
— параметров;
— качества металла оборудования.
Эксплуатационная надежность оборудования закладывается уже на стадии его проектирования и изготовления. Очевидно, что чем более высококачественный металл, тем больший запас прочности и износостойкости отдельных узлов; чем больше резерв вспомогательного оборудования, тем меньше будет вероятность аварийного недоотпуска энергии потребителям и величина внешнего ущерба. Но при этом возрастают капиталовложения и затраты, связанные с обеспечением надежности.

Современные методы позволяют спроектировать и изготовить энергетические установки сколь угодно высокой надежности. Однако такая установка будет иметь очень большой вес, габариты и стоимость. Очевидно, что при проектировании должна ставиться цель создания установки с некоторой оптимальной степенью надежности. Для установления оптимальности необходим критерий качества. Таким критерием для энергетических установок является критерий приведенных затрат, согласно этому критерию, установка является оптимальной, если при прочих равных условиях суммарная стоимость ее изготовления, эксплуатации и проектирования минимальна.
Однако одного критерия минимума стоимости бывает недостаточно при разработке технических требований к надежности установки и системы.
Требования к уровню надежности, разработанные на основе критерия минимума приведенных затрат, могут оказаться настолько высокими, а надежность настолько низкой, что удовлетворить этим требованиям, не прибегая к специальным мерам повышения надежности, не представляется возможным.
Характерный пример. Среднее время безотказной работы системы питания котла должно находиться в пределах 7000-8000 часов ( время между профилактическими ремонтами). Это условие означает, что интенсивность отказов этой системы должна быть на уровне:
λ = 1/T = (1/7000-1/8000) = (1.43-1.25)⋅10-4 (1/ч)
Современный паровой котел небольшой производительности имеет, по крайней мере, 4 питательных насоса. Интенсивность отказов питательных насосов (по данным фирмы Бабкок) составляет 0,419⋅10-4 1/ч.
В этом случае интенсивность отказов системы питания котла будет равна:
λсис.пит.= nλ = 4 ⋅ 0,419⋅10-4 = 1,676⋅10-4 (1/ч).
Т.е. надежность питательных насосов ниже требований, предъявляемых к системе питания.
В качестве критерия оптимальности решения устанавливаются расчетные (приведенные) затраты, руб/год, при производстве технологической продукции заданного качества и при обеспечении требуемой годовой производительности (Ргод = idem).
З = k ⋅ Eн + S,
где k – капитальные затраты, руб;
Eн – нормативный коэффициент эффективности капитальных вложений, 1/год;
S – издержки производства при эксплуатации, руб/год.
Минимуму приведенных затрат соответствует оптимальная надежность объекта.
Поскольку надежность объекта как системы элементов определяется в первую очередь наименее надежными элементами, то следует, прежде всего, повышать именно их надежность.
Повышение надежности элементов объекта, как отмечалось выше, возможно:
— путем использования более качественных конструкционных материалов типового оборудования при неизменной структуре установки и числе ее элементов;
— путем дублирования части элементов прежнего качества.
Возможна также комбинация обоих указанных путей.
В общем случае при повышении надежности установки продлевается срок службы между ремонтами, увеличивается вероятность безотказной работы и общая длительность работы в течение года. При этом требуемое число установок для обеспечения требуемой годовой производительности (Ргод = idem) уменьшается.
N = Pгод/Pустz
где Pуст – производительность одной установки;
z – число часов работы установки в году, ч/год.
z = 8760/(1 + Tрем/Tр) = 8760/(1 + Tремλ)
где Трем и Тр – длительность ремонта и межремонтной рабочей компании установки, ч.
Распределение годового времени между ремонтами и работой объекта
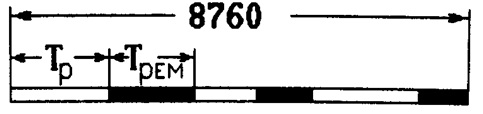
Одновременно возрастают капитальные затраты в каждую установку, изменяются амортизационные отчисления, расходы на ремонты и заработную плату. Остальные составляющие расчетных (приведенных) затрат не меняются и при решении задачи оптимизации могут не учитываться.
Изменяющаяся часть приведенных затрат руб/год.
З = k ⋅ Eн + Sам + Sрем + Sзпл (*)
Капитальные затраты, руб., при требуемом числе установок:
k = N ⋅kуст,
где kуст — капитальные затраты на одну установку, руб.
Расходы на ремонт установки
Sрем = N ⋅ nремSрем,
где nрем — число ремонтов одной установки в течение года, рем/год;
Sрем — стоимость одного ремонта установки, руб./рем.
Амортизационные отчисления:
Sам = NkустНа,
где На – норма амортизации, 1/год.
Расходы на заработную плату эксплуатационного персонала:
Sзпл = NSзпл,
где Sзпл — заработная плата, приходящаяся на одну установку в год, руб./уст.год.
Развернем выражение (*) для изменяющейся части приведенных затрат, подставив в него соответствующие составляющие.
З = N[(Eн + На)kуст + nремSрем + Sзпл] = Pгод/Pуст[(Eн + На)kуст + (8760-z)/TремSрем +
+ Sзпл] (**)
В зависимости от выбранного способа повышения надежности преобразование (**) дает то или иное выражение целевой функции для нахождения оптимального решения.